It has been a few years since I wrote Reloading 101 and I have commented several times that I should update it. Well I guess now is as good a time as any. This mental wandering is not comprehensive, it is “in addition to” the previous article. As always YRMV, IMHO, and other such bits as are required to ensure that you understand this is a thinking man’s game and I am merely making observations and defining MY experiences.
<span style="font-weight: bold">New Tools of the trade:</span> I linked to the manufacturer’s web site, as always you can shop for the best price at the usual suspects.
Hornady Sure-Loc-Lock Rings: Something as simple as a well designed piece of equipment can make a huge difference in your happiness factor when reloading. These lock Rings are simply the best in my opinion. The ring is a “compression” type in that it clamps around the die so that there are no set screws going into your dies, rubber o-rings or other such things. The best part is the wrench flats, a simple modification to a “normal” ring that makes a huge difference in usability.
http://www.hornady.com/store/Sure-Loc-Lock-Ring-6-Per-Pkg/
<span style="font-weight: bold">Stoney Point (now Hornady) Comparator Set:</span> This comparator set is the tool for measuring the ogive length of your rounds or the bullets themselves. The set comes with various insert for various bullet diameters. It clamps directly to your caliper and depending on your skill with calipers is very accurate. This tool is as essential to me for producing precision ammo as is the press. Remember when using this tool that your measurements will increase by 1” +/- due to the size of the tool.
http://www.hornady.com/store/Bullet-Comparator-Kits/
<span style="font-weight: bold">Stoney Point (now Hornady): Head and Shoulders gauges: </span> This simple bit of kit allows you to measure the headspace of your firearm via a fired case on your dial calipers. The set comes with various inserts that allow multiple cartridges to be investigated. The additional obvious benefit to the reloader is that it will allow you to precisely set up your dies to a known measurement as opposed to the abstract of “the bolt closes smoothly”. As above, the length of the tool must be taken into account when recording the length.
http://www.hornady.com/store/Headspace-Gauge-Kits/
<span style="font-weight: bold">Hornady Lock n Load Bushing Set:</span> The set consists of a bushing that you lock into your single stage press and three die collars that you screw/lock your dies into. It requires that your press has the 1-1/4 X 12 TPI opening (most single stage presses today have a bushing that can be unscrewed). This system is a Godsend and a pain all at the same time. The good part is that once you have all your dies set up the ability to change calibers is a simple twist of the wrist. The pain part is re-setting all of your dies to take advantage of the system. 10 packs of extra collars are available. I use paint or marker witness marks to ensure that the collets are fully turned into the bushing.
http://www.hornady.com/store/Bushings-c-457/
<span style="font-weight: bold">Redding Competition Shell Holders:</span> Redding makes a high precision set of shell holders that allow you to adjust the “crush” of the resize die or the tension of the seating die by simply changing the shell holder. The set consists of 5 shell holders: .002”, .004”, .006”, .008”, .010”. I set my dies up with the .006” shell holder, this allows me to add or subtract depth up to .004” from my “zero”. This is especially handy if you are reloading for multiple rifles of the same caliber and keeps you from resetting your dies for each. These shell holders are precision tools and are “snug” when pressing into your press ram. They may need a bit of “persuasion” to get into the ram.
http://www.redding-reloading.com/online-catalog/35-competition-shellholder-sets
<span style="font-weight: bold">Innovative Technologies Magnum Collet Die:</span> This die has been around for quite some time but I’m finally adding it into the mix for all the belted magnum shooters out there. Historically magnum brass will refuse to chamber after 3 – 5 reloads because of the expansion above the belt that factory dies will not fix. The concept of this die is as simple as it is effective. The die and collet allows you to squeeze the brass above the belt back down to “factory” size. The top of the die is a “brass checker”, basically if your brass fits you don’t have to size it. If it doesn’t, lube a case, slip on the collet and run it into the die. The instructions recommend Imperial Sizing wax as a lubricant. I have found that spray on lube’s are MUCH better. Probably because I did something wrong with the wax, the result was ripping off case heads and beating the brass out with a section of military cleaning rod. No matter how you go about it this die is a MUST HAVE for a belted magnum cartridge shooter that wants to get more than a hand full of loads out of their brass. NOTE: You will have to mount this die each time if you are using the Lock N Load Bushing Set since the base will not fit through the bushing on the press. Fortunately the set up is rather simple and doesn’t require precision location.
http://larrywillis.com/
<span style="font-weight: bold">Sinclair Chamber Length Gage:</span> This tool provides you the means to accurately determine how long the neck of your chamber is. It is simply a plug that is inserted into a shortened case that indexes at the end of your chamber. This will tell you how long you can let your brass “grow” before you NEED to trim as opposed to using the arbitrary “factory case length” numbers in a reloading manual. As with most things factory, chamber length is usually much longer than specification.
http://www.sinclairintl.com/.aspx/pid=32925/Product/Sinclair_Chamber_Length_Gage
<span style="font-weight: bold">Saturn Powder Funnel:</span> These powder funnels are simply the best that I have used. Due to the design, the funnels are sized so that you have to buy one for each caliber you are loading for. I find this a small price to pay for the resulting performance compared to a “universal”.
http://saternmachining.com/products
<span style="font-weight: bold">Sinclair Gen II Flash Hole Reamer:</span> In response to my major complaint that the RCBS flash hole reamer would get bound up with brass chips, Sinclair fixed it. They have designed a flash hole reamer that evacuates the chips yet still indexes on the web of the case so that you don’t have to trim all your brass to the same length prior to reaming the flash hole.
http://www.sinclairintl.com/.aspx/pid=34127/Product/Gen_II_Universal_FlashHole_Deburring_Tool
<span style="font-weight: bold">100 yard Tape Measure: </span> Absolutely invaluable for marking off yard lines and for optically checking your rifle scope.
http://www.cooperhandtools.com/brands/CF_Files/model_detail.cfm?upc=037103224118
Other bits:
<span style="font-weight: bold">What to do if the brass fits:</span> Many times when we begin reloading for a rifle we will use new brass or brass that fits in the chamber without the benefit of resizing at all. This creates a quandary as to how to set up the dies to find the minimum amount of resizing. Often times it takes 1 – 3 firings of new brass (or new to the rifle) to get it to the point that it won’t fit in our chamber. Getting it to that point is difficult if we set up the dies to resize the case straight out of the box. The trick here is to resize the case only enough to get the bullet to hold on the seating process.
Once again it is time for “Ye’ old Sharpie”. Color the top your case from the mouth down to about ¼” past the shoulder. Back the die out of the press until you barely feel any resistance at full throw. Turn the die down a ½ - ¼ of a turn at a time until you start to see the resizing die scuff the shoulder of the brass. You should have the neck almost fully resized by this time. Lock the die down.
If you are keeping notes (and you should be) record the headspace length with your Head and Shoulders measuring set and go shoot. When you return you may or may not find that the case still chambers easily in your rifle. If it still chambers, color the shoulder and body again and see if the case is scuffed by the die. If it is, back the die out until you get to the point where it’s just not being scuffed and lock the die down and record your findings (don’t forget to cross out the previous measurements). You may have to repeat this operation several times to get the marker on the brass to be un-scuffed.
Once you let the brass grow by firing until it won’t chamber or chambers with resistance, you can adjust the die so that the brass will “just” close smoothly or with a “slight” bit of compression or none at all. Resize several pieces of brass to ensure that the brass is consistent and will feed smoothly, there is spring back even in resize dies. Personally I like the bolt to close with no resistance as ambient weather conditions and chamber temperatures can change the dimensions of your brass slightly. Now is also the time to revisit all of your die settings to ensure that you are sizing the brass to the minimum amount, not only in the resizing operation but also in the bullet seating operation. Once again the Head and Shoulders as well as your Bullet Comparator tools will provide you with hard data as to what your dies are doing to your brass. Record your final findings, mark them as final, don’t forget the date.
<span style="font-weight: bold">A Note on Notes:</span> As with most things precision, especially in the rifle world it is handy to have notes regarding what it is you are doing. To this end I have made up a simple drawing that allows me to quickly annotate the various dimensions of the cartridge I’m working on or more importantly the chamber it’s going into. It also gives me a place to record my load data once everything is finalized. These notes become important if you shoot several different rifles or don’t reload for a length of time. Combining this with the data from your rifle data book(s) you can keep track of any changes that occur in your rifle that require a modification of your load. For instance, you may need to adjust the ogive length of your cartridge to maintain accuracy as your barrel wears.
<span style="font-weight: bold">Poor Man’s Stuck Case Remover:</span> If you reload for any length of time, sooner or later you will get a stuck case. It happens. Generally you notice the case is stuck AFTER you have ripped the rim off the case. Often time’s reloaders will be tempted to unscrew the decapping pin lock nut and drive the case out with a beating stick of some sort. The end result of this effort is usually a bent decapping rod and or broken pin which really puts a crimp in your day. The way most resize/decapping dies are set up you should be able to unscrew the decapping rod from the die and get the pin out of the flash hole. From here it is simply a matter of drilling a larger hole in your brass so you can tap it to accommodate a machine screw/bolt of some type.
In general I use a ¼” – 20 TPI tap with a 13/64ths or #7 drill bit. Once you have the hole bored out and the threads put in it is a matter of using one fender washer and a 3/8” drive socket that fits on the shoulder of the die but not on the case (a ½” socket works well for .308 and smaller case heads). On some case/die combo’s you may need a socket that will rest on the lock nut (a 7/8” deep well usually works) if there isn’t sufficient room on the die shoulder for the socket. Put the screw / bolt in the fender washer and put them into the socket base and then screw it into the case. Using the appropriate wrench it will draw the case out of the die. You can either put the die in a vice or put it back in the press as you probably will not be able to draw the case out by holding the die in your hand. I keep a dedicated set of these tools in my reloading stuff so I don’t have to hunt around the workshop to find a washer, bolt, socket and my tap set which just adds to the frustration of the moment.
<span style="font-weight: bold">Bullet Comparo or “The Ogive story”:</span> Much has been discussed regarding the relative merits of seating bullets to ogive length verses just seating to Over All Length (OAL) or more specifically SAAMI OAL. This came into sharp relief recently when helping a new reloader develop ammo for his new rifle. In this particular case a 300WM. SAAMI OAL for the 300WM is insanely short IMHO and most factory chambers (Remington in this case) are far and away longer than the SAAMI specs. We found the lands via the Sharpie and chamber method. The end result was an OAL about 0.30” longer than the reloading manual said it should be. This never even raised an eyebrow from me as I expected as much.
My new reloader called me in a panic the next day thinking that we had done something wrong in the process (probably also thinking that I was going senile). I was fairly certain that we hadn’t but it caused me to revisit the procedures and double check the notes that I had taken. Better safe than sorry and I’m not above admitting when I screwed up. The result was that I hadn’t screwed up and that he had ammo custom fit to his rifle chamber, as was the intent. It just didn’t match the book, which is what caused his distress.
Ogive length loading is vital to the consistency of the reloading process. Since we know that total bullet length versus ogive length is not consistent from box to box (or even from bullet to bullet in the same box) measuring the OAL is not beneficial to consistency. Ogive measuring ensures that the amount of “jump” or “crush” is consistent in relation to the bullet and leade interface (the leade is where the lands start).
One problem that may be encountered is when the leade is so far down the barrel that the cartridge will not fit into the magazine box or the magazine proper. The choices at that time are to make ammo to be single loaded or make it so that it fits in the magazine with a consistent amount of jump. The only other choice is to have the barrel set back and rechambered, but that’s not what we’re looking at here. When doing load development I will often find the lands and then push the bullet back 0.010” and use that as a baseline while playing with powder charges. Once I find the appropriate powder charge I will then play with the Ogive Length to “round out” the groups. Often times it will also significantly shrink the group size.
<span style="font-weight: bold">Full length resizing:</span> I am still convinced that full length resizing is the way to go for reloading ALL rifle and pistol brass for most reloaders. The primary focus of resizing is to ensure 100% reliability of feeding and chambering, PERIOD. My contention is based on the concept that I may be in a situation that requires a rapid feed/chamber and I should not have to consider that due to the vagaries of machining and ambient conditions that I may not be able to close the bolt.
Bushing dies do present an interesting argument but as with the pretext of this article I’m looking for cost vs. benefit. The principle behind a bushing die is that you can control the neck tension of the brass via interchangeable bushings. OK I’ll buy that, but what happens when you change brass or your brass grows and you have to trim? Where did the brass you trimmed off come from? Simply put you’ll need additional bushings for various conditions and brass, AND you’ll have to figure out when to use them. As before I feel that with the absence of resizing the interior of the neck via a mandrel and subsequent external neck turning a bushing die has little to no advantage over a conventional die. As much as I dislike trimming the length I’m thinking I’d enjoy trimming the neck even less. Cost vs benefit and time & effort, you’ll have to decide if it is worth it to you.
<span style="font-weight: bold">Expanders: balls, ovals and rods:</span> I have done some significant experimenting with the concept of expanders in the process of resizing. The purpose of an expander ball, oval or rod is to ensure that the inside diameter of the neck of the cartridge is consistent and that the inside of the neck is round. The problem that is encountered during resizing with an expander is that the forces of friction on the neck often results in and inconsistent shoulder as the case is pulled back over the ball / oval. The variance is in small degrees and measurements, but it exists none the less. To try it yourself, pull the expander ball and measure the headspace length of a resized cartridge vs. the one with the ball. The most consistent fix is to lightly polish the expander ball to a bright finish and adjust the ball so that at full resize it is just below the neck/shoulder junction. (DO NOT get the ball into the neck it will mechanically lock your die up.) This is where I find the least impact and most consistent and minimal change to the headspace length.
The cure would be to have a “resizing rod” that resizes the inside of the neck at the same time the case is pushed all the way into the die. Unfortunately I have yet to find one that works “universally”, as this essentially would be a “forming” die. This concept would create many additional issues to deal with, most significantly the mechanical “lock” that would result from the process. The Lee resizing die expanders are the closest to this concept and are very effective.
<span style="font-weight: bold">Books, Reloading Manuals and CD’s (Knowledge is power):</span> The need has not changed; reference material is required to perform this pursuit to any degree of success. The information however has progressed insomuch as technology, cartridges, powder and projectiles have progressed. Current manuals are significantly advantageous when dealing with new components. That being said old versions of manuals are singularly interesting for their comparative aspects. Somewhere along the line I mentioned to a friend of mine “never throw away an old manual”. He recently commented on finding the use of a particular powder for his 280AI in a 1988 manual that is no longer discussed in current manuals. This powder turned out to have all the qualities he was looking for as well as some significant velocity and consistency gains. As with anything in marketing NEW is improved and therefore must be better (cough, cough), “old” is sometimes cast out as newer things fill up the pages of current texts. Remember, anything in print regarding reloading is scrutinized by lawyers to ensure the non-liability of the company. Standard cautionary statements of “start low and work up” apply here.
<span style="font-weight: bold">Volume vs Speed:</span> I have noticed in many manuals that the faster powders will provide some advantage in speed but at the cost of case powder fill. It has been my experience, and now my pursuit, to match a powder to the fill volume of the charge. I like my powder charge to be right up near the neck/shoulder junction. This combined with bullet seating gives me nearly a 100% case fill. The effect is a much more consistent velocity as proven by the chronograph. Most of my velocity spreads are in the low “teens” for a 10 shot test. A recent test with a new powder certainly showed significant velocity increases but the case fill resulted in an ES of 63 fps, too much for my tastes to run the long line.
A Note on ES and chronographs: The better chronographs out there have a velocity error factor of 0.005 +/- fps. Pretty small right? Multiply that times 2700 (or your average velocity) and you will get 13.5. This tells me that an ES of less than 13.5 is within the error value of the chronograph. Something to think about.
As you read this you will probably wave figured out that I continue to look for better mouse traps and tools to improve or speed up my reloading efforts, hence the new bits of kit. I also addressed some reoccurring questions that were brought up from Reloading 101. I hope you enjoyed reading it as much as I enjoyed writing it.
Cheers,
Doc
<span style="font-weight: bold">New Tools of the trade:</span> I linked to the manufacturer’s web site, as always you can shop for the best price at the usual suspects.
Hornady Sure-Loc-Lock Rings: Something as simple as a well designed piece of equipment can make a huge difference in your happiness factor when reloading. These lock Rings are simply the best in my opinion. The ring is a “compression” type in that it clamps around the die so that there are no set screws going into your dies, rubber o-rings or other such things. The best part is the wrench flats, a simple modification to a “normal” ring that makes a huge difference in usability.
http://www.hornady.com/store/Sure-Loc-Lock-Ring-6-Per-Pkg/
<span style="font-weight: bold">Stoney Point (now Hornady) Comparator Set:</span> This comparator set is the tool for measuring the ogive length of your rounds or the bullets themselves. The set comes with various insert for various bullet diameters. It clamps directly to your caliper and depending on your skill with calipers is very accurate. This tool is as essential to me for producing precision ammo as is the press. Remember when using this tool that your measurements will increase by 1” +/- due to the size of the tool.
http://www.hornady.com/store/Bullet-Comparator-Kits/
<span style="font-weight: bold">Stoney Point (now Hornady): Head and Shoulders gauges: </span> This simple bit of kit allows you to measure the headspace of your firearm via a fired case on your dial calipers. The set comes with various inserts that allow multiple cartridges to be investigated. The additional obvious benefit to the reloader is that it will allow you to precisely set up your dies to a known measurement as opposed to the abstract of “the bolt closes smoothly”. As above, the length of the tool must be taken into account when recording the length.
http://www.hornady.com/store/Headspace-Gauge-Kits/
<span style="font-weight: bold">Hornady Lock n Load Bushing Set:</span> The set consists of a bushing that you lock into your single stage press and three die collars that you screw/lock your dies into. It requires that your press has the 1-1/4 X 12 TPI opening (most single stage presses today have a bushing that can be unscrewed). This system is a Godsend and a pain all at the same time. The good part is that once you have all your dies set up the ability to change calibers is a simple twist of the wrist. The pain part is re-setting all of your dies to take advantage of the system. 10 packs of extra collars are available. I use paint or marker witness marks to ensure that the collets are fully turned into the bushing.
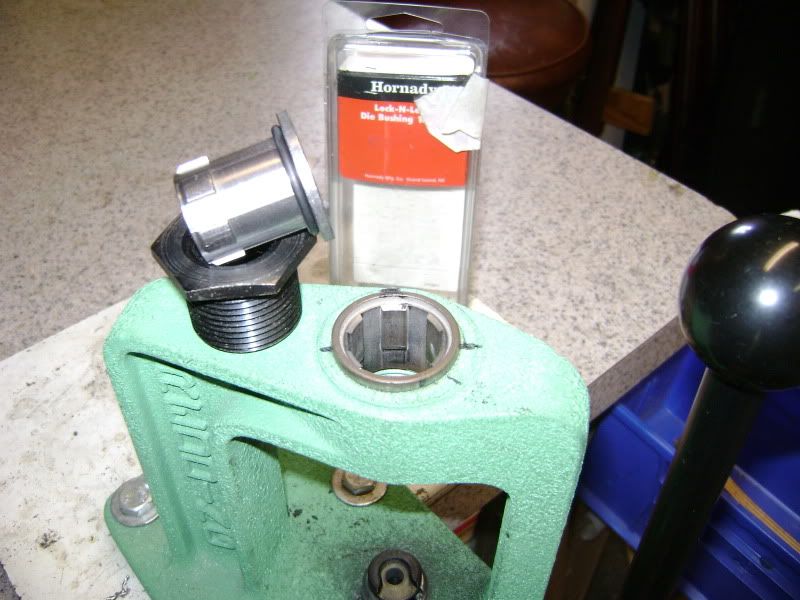
http://www.hornady.com/store/Bushings-c-457/
<span style="font-weight: bold">Redding Competition Shell Holders:</span> Redding makes a high precision set of shell holders that allow you to adjust the “crush” of the resize die or the tension of the seating die by simply changing the shell holder. The set consists of 5 shell holders: .002”, .004”, .006”, .008”, .010”. I set my dies up with the .006” shell holder, this allows me to add or subtract depth up to .004” from my “zero”. This is especially handy if you are reloading for multiple rifles of the same caliber and keeps you from resetting your dies for each. These shell holders are precision tools and are “snug” when pressing into your press ram. They may need a bit of “persuasion” to get into the ram.
http://www.redding-reloading.com/online-catalog/35-competition-shellholder-sets
<span style="font-weight: bold">Innovative Technologies Magnum Collet Die:</span> This die has been around for quite some time but I’m finally adding it into the mix for all the belted magnum shooters out there. Historically magnum brass will refuse to chamber after 3 – 5 reloads because of the expansion above the belt that factory dies will not fix. The concept of this die is as simple as it is effective. The die and collet allows you to squeeze the brass above the belt back down to “factory” size. The top of the die is a “brass checker”, basically if your brass fits you don’t have to size it. If it doesn’t, lube a case, slip on the collet and run it into the die. The instructions recommend Imperial Sizing wax as a lubricant. I have found that spray on lube’s are MUCH better. Probably because I did something wrong with the wax, the result was ripping off case heads and beating the brass out with a section of military cleaning rod. No matter how you go about it this die is a MUST HAVE for a belted magnum cartridge shooter that wants to get more than a hand full of loads out of their brass. NOTE: You will have to mount this die each time if you are using the Lock N Load Bushing Set since the base will not fit through the bushing on the press. Fortunately the set up is rather simple and doesn’t require precision location.
http://larrywillis.com/
<span style="font-weight: bold">Sinclair Chamber Length Gage:</span> This tool provides you the means to accurately determine how long the neck of your chamber is. It is simply a plug that is inserted into a shortened case that indexes at the end of your chamber. This will tell you how long you can let your brass “grow” before you NEED to trim as opposed to using the arbitrary “factory case length” numbers in a reloading manual. As with most things factory, chamber length is usually much longer than specification.
http://www.sinclairintl.com/.aspx/pid=32925/Product/Sinclair_Chamber_Length_Gage
<span style="font-weight: bold">Saturn Powder Funnel:</span> These powder funnels are simply the best that I have used. Due to the design, the funnels are sized so that you have to buy one for each caliber you are loading for. I find this a small price to pay for the resulting performance compared to a “universal”.
http://saternmachining.com/products
<span style="font-weight: bold">Sinclair Gen II Flash Hole Reamer:</span> In response to my major complaint that the RCBS flash hole reamer would get bound up with brass chips, Sinclair fixed it. They have designed a flash hole reamer that evacuates the chips yet still indexes on the web of the case so that you don’t have to trim all your brass to the same length prior to reaming the flash hole.
http://www.sinclairintl.com/.aspx/pid=34127/Product/Gen_II_Universal_FlashHole_Deburring_Tool
<span style="font-weight: bold">100 yard Tape Measure: </span> Absolutely invaluable for marking off yard lines and for optically checking your rifle scope.
http://www.cooperhandtools.com/brands/CF_Files/model_detail.cfm?upc=037103224118
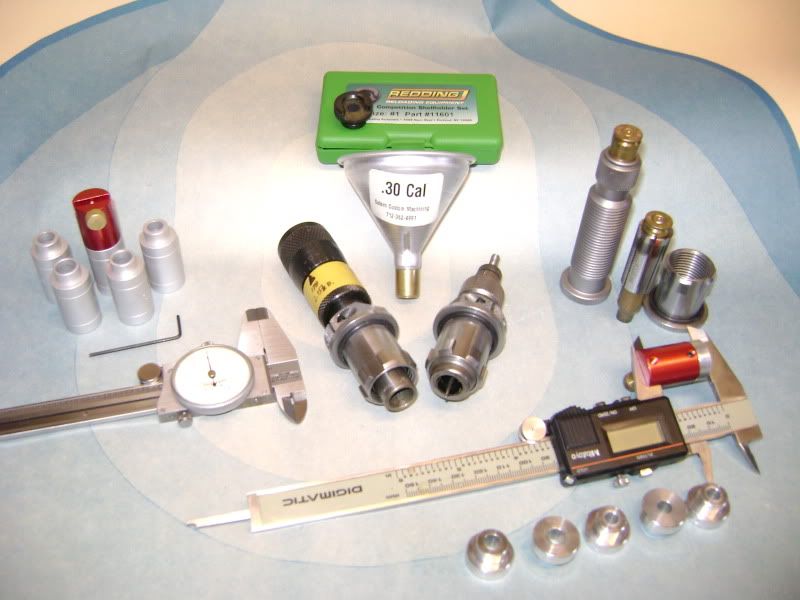
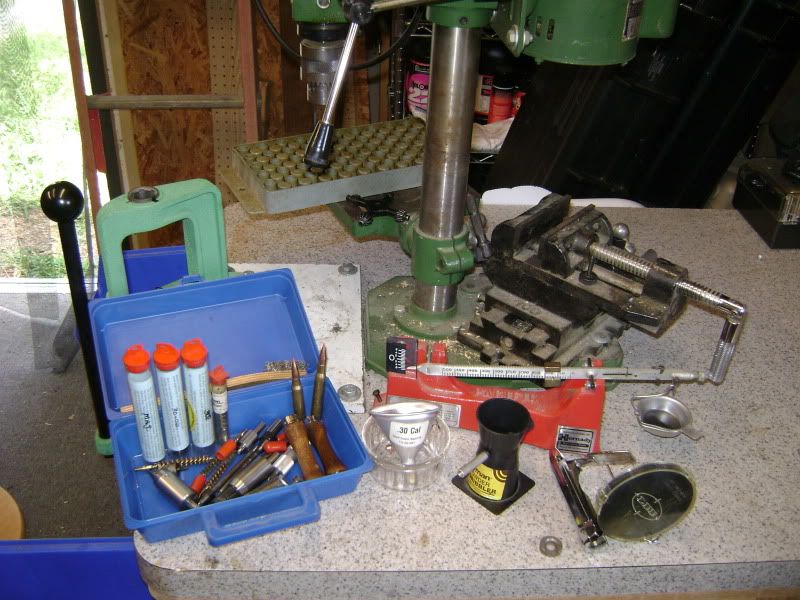
Other bits:
<span style="font-weight: bold">What to do if the brass fits:</span> Many times when we begin reloading for a rifle we will use new brass or brass that fits in the chamber without the benefit of resizing at all. This creates a quandary as to how to set up the dies to find the minimum amount of resizing. Often times it takes 1 – 3 firings of new brass (or new to the rifle) to get it to the point that it won’t fit in our chamber. Getting it to that point is difficult if we set up the dies to resize the case straight out of the box. The trick here is to resize the case only enough to get the bullet to hold on the seating process.
Once again it is time for “Ye’ old Sharpie”. Color the top your case from the mouth down to about ¼” past the shoulder. Back the die out of the press until you barely feel any resistance at full throw. Turn the die down a ½ - ¼ of a turn at a time until you start to see the resizing die scuff the shoulder of the brass. You should have the neck almost fully resized by this time. Lock the die down.
If you are keeping notes (and you should be) record the headspace length with your Head and Shoulders measuring set and go shoot. When you return you may or may not find that the case still chambers easily in your rifle. If it still chambers, color the shoulder and body again and see if the case is scuffed by the die. If it is, back the die out until you get to the point where it’s just not being scuffed and lock the die down and record your findings (don’t forget to cross out the previous measurements). You may have to repeat this operation several times to get the marker on the brass to be un-scuffed.
Once you let the brass grow by firing until it won’t chamber or chambers with resistance, you can adjust the die so that the brass will “just” close smoothly or with a “slight” bit of compression or none at all. Resize several pieces of brass to ensure that the brass is consistent and will feed smoothly, there is spring back even in resize dies. Personally I like the bolt to close with no resistance as ambient weather conditions and chamber temperatures can change the dimensions of your brass slightly. Now is also the time to revisit all of your die settings to ensure that you are sizing the brass to the minimum amount, not only in the resizing operation but also in the bullet seating operation. Once again the Head and Shoulders as well as your Bullet Comparator tools will provide you with hard data as to what your dies are doing to your brass. Record your final findings, mark them as final, don’t forget the date.
<span style="font-weight: bold">A Note on Notes:</span> As with most things precision, especially in the rifle world it is handy to have notes regarding what it is you are doing. To this end I have made up a simple drawing that allows me to quickly annotate the various dimensions of the cartridge I’m working on or more importantly the chamber it’s going into. It also gives me a place to record my load data once everything is finalized. These notes become important if you shoot several different rifles or don’t reload for a length of time. Combining this with the data from your rifle data book(s) you can keep track of any changes that occur in your rifle that require a modification of your load. For instance, you may need to adjust the ogive length of your cartridge to maintain accuracy as your barrel wears.
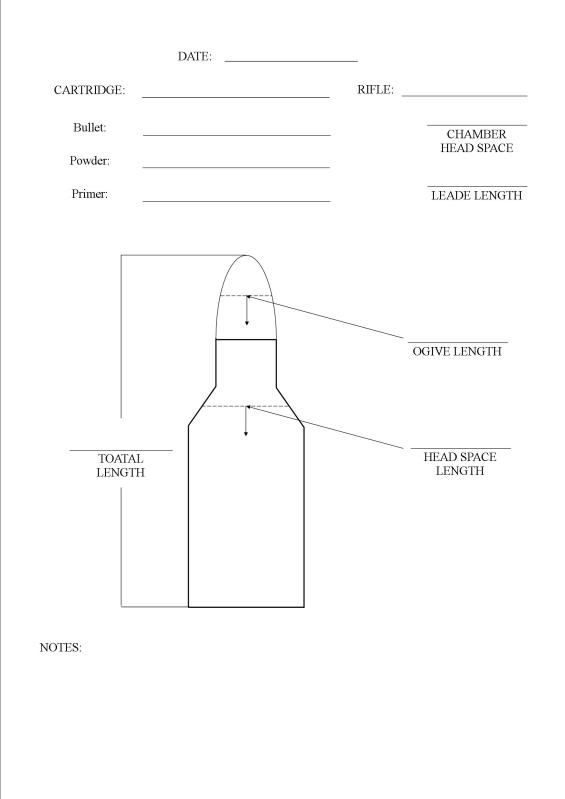
<span style="font-weight: bold">Poor Man’s Stuck Case Remover:</span> If you reload for any length of time, sooner or later you will get a stuck case. It happens. Generally you notice the case is stuck AFTER you have ripped the rim off the case. Often time’s reloaders will be tempted to unscrew the decapping pin lock nut and drive the case out with a beating stick of some sort. The end result of this effort is usually a bent decapping rod and or broken pin which really puts a crimp in your day. The way most resize/decapping dies are set up you should be able to unscrew the decapping rod from the die and get the pin out of the flash hole. From here it is simply a matter of drilling a larger hole in your brass so you can tap it to accommodate a machine screw/bolt of some type.
In general I use a ¼” – 20 TPI tap with a 13/64ths or #7 drill bit. Once you have the hole bored out and the threads put in it is a matter of using one fender washer and a 3/8” drive socket that fits on the shoulder of the die but not on the case (a ½” socket works well for .308 and smaller case heads). On some case/die combo’s you may need a socket that will rest on the lock nut (a 7/8” deep well usually works) if there isn’t sufficient room on the die shoulder for the socket. Put the screw / bolt in the fender washer and put them into the socket base and then screw it into the case. Using the appropriate wrench it will draw the case out of the die. You can either put the die in a vice or put it back in the press as you probably will not be able to draw the case out by holding the die in your hand. I keep a dedicated set of these tools in my reloading stuff so I don’t have to hunt around the workshop to find a washer, bolt, socket and my tap set which just adds to the frustration of the moment.
<span style="font-weight: bold">Bullet Comparo or “The Ogive story”:</span> Much has been discussed regarding the relative merits of seating bullets to ogive length verses just seating to Over All Length (OAL) or more specifically SAAMI OAL. This came into sharp relief recently when helping a new reloader develop ammo for his new rifle. In this particular case a 300WM. SAAMI OAL for the 300WM is insanely short IMHO and most factory chambers (Remington in this case) are far and away longer than the SAAMI specs. We found the lands via the Sharpie and chamber method. The end result was an OAL about 0.30” longer than the reloading manual said it should be. This never even raised an eyebrow from me as I expected as much.
My new reloader called me in a panic the next day thinking that we had done something wrong in the process (probably also thinking that I was going senile). I was fairly certain that we hadn’t but it caused me to revisit the procedures and double check the notes that I had taken. Better safe than sorry and I’m not above admitting when I screwed up. The result was that I hadn’t screwed up and that he had ammo custom fit to his rifle chamber, as was the intent. It just didn’t match the book, which is what caused his distress.
Ogive length loading is vital to the consistency of the reloading process. Since we know that total bullet length versus ogive length is not consistent from box to box (or even from bullet to bullet in the same box) measuring the OAL is not beneficial to consistency. Ogive measuring ensures that the amount of “jump” or “crush” is consistent in relation to the bullet and leade interface (the leade is where the lands start).
One problem that may be encountered is when the leade is so far down the barrel that the cartridge will not fit into the magazine box or the magazine proper. The choices at that time are to make ammo to be single loaded or make it so that it fits in the magazine with a consistent amount of jump. The only other choice is to have the barrel set back and rechambered, but that’s not what we’re looking at here. When doing load development I will often find the lands and then push the bullet back 0.010” and use that as a baseline while playing with powder charges. Once I find the appropriate powder charge I will then play with the Ogive Length to “round out” the groups. Often times it will also significantly shrink the group size.
<span style="font-weight: bold">Full length resizing:</span> I am still convinced that full length resizing is the way to go for reloading ALL rifle and pistol brass for most reloaders. The primary focus of resizing is to ensure 100% reliability of feeding and chambering, PERIOD. My contention is based on the concept that I may be in a situation that requires a rapid feed/chamber and I should not have to consider that due to the vagaries of machining and ambient conditions that I may not be able to close the bolt.
Bushing dies do present an interesting argument but as with the pretext of this article I’m looking for cost vs. benefit. The principle behind a bushing die is that you can control the neck tension of the brass via interchangeable bushings. OK I’ll buy that, but what happens when you change brass or your brass grows and you have to trim? Where did the brass you trimmed off come from? Simply put you’ll need additional bushings for various conditions and brass, AND you’ll have to figure out when to use them. As before I feel that with the absence of resizing the interior of the neck via a mandrel and subsequent external neck turning a bushing die has little to no advantage over a conventional die. As much as I dislike trimming the length I’m thinking I’d enjoy trimming the neck even less. Cost vs benefit and time & effort, you’ll have to decide if it is worth it to you.
<span style="font-weight: bold">Expanders: balls, ovals and rods:</span> I have done some significant experimenting with the concept of expanders in the process of resizing. The purpose of an expander ball, oval or rod is to ensure that the inside diameter of the neck of the cartridge is consistent and that the inside of the neck is round. The problem that is encountered during resizing with an expander is that the forces of friction on the neck often results in and inconsistent shoulder as the case is pulled back over the ball / oval. The variance is in small degrees and measurements, but it exists none the less. To try it yourself, pull the expander ball and measure the headspace length of a resized cartridge vs. the one with the ball. The most consistent fix is to lightly polish the expander ball to a bright finish and adjust the ball so that at full resize it is just below the neck/shoulder junction. (DO NOT get the ball into the neck it will mechanically lock your die up.) This is where I find the least impact and most consistent and minimal change to the headspace length.
The cure would be to have a “resizing rod” that resizes the inside of the neck at the same time the case is pushed all the way into the die. Unfortunately I have yet to find one that works “universally”, as this essentially would be a “forming” die. This concept would create many additional issues to deal with, most significantly the mechanical “lock” that would result from the process. The Lee resizing die expanders are the closest to this concept and are very effective.
<span style="font-weight: bold">Books, Reloading Manuals and CD’s (Knowledge is power):</span> The need has not changed; reference material is required to perform this pursuit to any degree of success. The information however has progressed insomuch as technology, cartridges, powder and projectiles have progressed. Current manuals are significantly advantageous when dealing with new components. That being said old versions of manuals are singularly interesting for their comparative aspects. Somewhere along the line I mentioned to a friend of mine “never throw away an old manual”. He recently commented on finding the use of a particular powder for his 280AI in a 1988 manual that is no longer discussed in current manuals. This powder turned out to have all the qualities he was looking for as well as some significant velocity and consistency gains. As with anything in marketing NEW is improved and therefore must be better (cough, cough), “old” is sometimes cast out as newer things fill up the pages of current texts. Remember, anything in print regarding reloading is scrutinized by lawyers to ensure the non-liability of the company. Standard cautionary statements of “start low and work up” apply here.
<span style="font-weight: bold">Volume vs Speed:</span> I have noticed in many manuals that the faster powders will provide some advantage in speed but at the cost of case powder fill. It has been my experience, and now my pursuit, to match a powder to the fill volume of the charge. I like my powder charge to be right up near the neck/shoulder junction. This combined with bullet seating gives me nearly a 100% case fill. The effect is a much more consistent velocity as proven by the chronograph. Most of my velocity spreads are in the low “teens” for a 10 shot test. A recent test with a new powder certainly showed significant velocity increases but the case fill resulted in an ES of 63 fps, too much for my tastes to run the long line.
A Note on ES and chronographs: The better chronographs out there have a velocity error factor of 0.005 +/- fps. Pretty small right? Multiply that times 2700 (or your average velocity) and you will get 13.5. This tells me that an ES of less than 13.5 is within the error value of the chronograph. Something to think about.
As you read this you will probably wave figured out that I continue to look for better mouse traps and tools to improve or speed up my reloading efforts, hence the new bits of kit. I also addressed some reoccurring questions that were brought up from Reloading 101. I hope you enjoyed reading it as much as I enjoyed writing it.
Cheers,
Doc