F
free_rider_151
Guest
Howdy everyone! I'm new to posting here. I've been reading this forum for a few years now and I think it's the best place to find a good average of information.
I have been shooting a 300 rum for the last 3 years or so. Thus far I had only taken it to 700 yards. I was uneasy about the stock remington action so I decided to have it worked over by Montour County Rifles. I got it chambered in 338 Edge and I am eagerly awaiting it's arrival next week. I am an avid reloader and have done smith work on a number of bolt actions, semis, and pistols. I work for a company that measures, scans, and 3D models anything you can imagine. Now that you know a little bit about me and my background, let’s get into the details of my theory.
Extreme Long Range Cartridges (henceforth ELRC) follow a set of linear characteristic factors. While there are some constants, each ELRC has a progressive yet predictable change in dimension from one chambering to another.
Let’s take a quick look at internal ballistics for a moment and define the primary characteristics of the reaction involved in burning rifle powder.
When the firing pin strikes the primer it ignites the primary explosive and creates a very high velocity shockwave that propagates through the flash hole and into the ELRC. This shockwave is complimented by extreme heat and pressure that in turn ignites the rifle powder. The point of the rifle powder ignition is in the most rearward end of the ELRC and propagates in a semi elliptical shape down the length of the ELRC. This action of deflagration creates a wave of pressure and heat.
For my first linear characteristic element, I will attempt to show how a solid rocket motor is analogous to an ELRC.
1. Ignition Bulk Head (farthest left end of the picture below.)
2. Fuel Grain
3. Nozzle
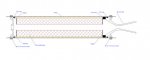
ELRCs have the same general layout and principal model of operation as that of a high power solid rocket motor.
Let’s look at the point of ignition.
On both the motor and ELRC, the point of ignition is opposite the nozzle end.
Rocket motor: The reason for ignition at the top of the motor is due to the considerably faster rate at which the propellant grain is fully ignited. This is because the high pressure/high temperature gases are only able to escape through the nozzle of the motor, therefore, the flame channel burns downwards, not upwards.
ELRC: The point of ignition located in the rearward most end is due to simplicity of adaptation. However, later I will explain why this characteristic is so important to future ELRC development.
Let’s look at the propellant charge.
ELRC: The powder is burnt in an elliptical wave front that moves down the length of the cartridge. Not all of the powder is burnt in the cartridge however. Because the wave is creating pressure at the rear of the cartridge, this pushes the remaining powder against the projectile and pushes it out of the cartridge. As the wave front pushes the powder and projectile down the barrel, the powder is consumed. Because the powder is burning in a single wave plane, the surface area remains constant with the exception of the change of the diameter from body to bore.
Let’s look at the nozzle/neck:
Design characteristic similarities
The inherit similarity in ignition position affords us the luxury of easy development of solid single grain rifle propellants. The physical restriction of rifle powder to the area of the cartridge allows us to take advantage of controllable burning surface area (constant or adaptive pressure transient) and convergent nozzle gas acceleration. In general, rockets reach flight speed and hold somewhat steady at a velocity until the grain becomes structurally unstable and begins to burn out. This requires a constant pressure to avoid detonation during flight. Both rifle powder and rocket fuel burn at a rate that is proportional to the ambient pressure. This means that if a rocket nozzle is too small or a rifle bore is too small, it will build pressure exponentially until it exceeds that of the containing vessel (rocket motor case/rifle chamber). I have witnessed this first hand from 3 feet away when a kno3 rocket motor detonated at upwards of 150000 psi. Lots of blood and a few stitches inevitably followed.
In a rifle however, as the bullet is accelerated down the barrel, the volume for the expanding gases increases proportionally with the projectile velocity. This means that a constant propellant burn rate creates a downward sloping pressure transient. This, in effect, means the projectile acceleration slows down proportionally to the distance from the throat.
With this in mind, it would be advantageous for the design of an ELRC to incorporate an accelerating rate of propellant consumption to make projectile acceleration constant. I have tried several different experiments with this, but thus far, none have been acceptably safe or effective. In doing research on military experiments and development of current munitions, I have come up with a reasonable solution that is tried and currently in use across the world. I will discuss this in summary at the end.
The next linear characteristic design element is the optimization limits of ELRC’s
Optimization of current cartridges with current technology
The other aspect that effects the efficiency difference in tank rounds is that the propellant is for the most part (from what little I know) contained and burned in the cartridge. This allows the subsonic propellant gases to be accelerated in the convergent bottleneck section to bore velocities high enough to achieve 5200fps+. Incorporating fixed propellant in ELR rounds will not only effect a higher muzzle velocity, but will also reduce fouling. When the powder in conventional ELRC’s is burned down the bore, it deposits carbon and binding compounds in the rifling. This fouling can be minimized by the extreme temperatures exhibited at the convergent bottleneck of the cartridge. Because of the flame pressure front burning in a radial direction, the binding compounds would be more prone to affixing themselves to the cartridge wall. This will increase barrel life, aswell as increasing the intervals between cleaning.
In summary
Ok, so I’ve been writing this for the last 5 hours… so I’m getting tired and lazy. Hence the 1 sentence summary.
Please correct me on any facts I may have wrong. I’m no expert on this, so there are bound to be flaws in my logic. If you have any insight into my theory, please speak up. I want to begin development of an extremely efficient scalable round for elr. Thanks for sticking with me and reading this…. If you made it to the end, you have a longer attention span than me…..
I have been shooting a 300 rum for the last 3 years or so. Thus far I had only taken it to 700 yards. I was uneasy about the stock remington action so I decided to have it worked over by Montour County Rifles. I got it chambered in 338 Edge and I am eagerly awaiting it's arrival next week. I am an avid reloader and have done smith work on a number of bolt actions, semis, and pistols. I work for a company that measures, scans, and 3D models anything you can imagine. Now that you know a little bit about me and my background, let’s get into the details of my theory.
Extreme Long Range Cartridges (henceforth ELRC) follow a set of linear characteristic factors. While there are some constants, each ELRC has a progressive yet predictable change in dimension from one chambering to another.
Let’s take a quick look at internal ballistics for a moment and define the primary characteristics of the reaction involved in burning rifle powder.
When the firing pin strikes the primer it ignites the primary explosive and creates a very high velocity shockwave that propagates through the flash hole and into the ELRC. This shockwave is complimented by extreme heat and pressure that in turn ignites the rifle powder. The point of the rifle powder ignition is in the most rearward end of the ELRC and propagates in a semi elliptical shape down the length of the ELRC. This action of deflagration creates a wave of pressure and heat.
For my first linear characteristic element, I will attempt to show how a solid rocket motor is analogous to an ELRC.
In a solid rocket motor you have three parts:1. Ignition Bulk Head (farthest left end of the picture below.)
2. Fuel Grain
3. Nozzle
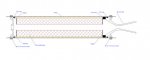
ELRCs have the same general layout and principal model of operation as that of a high power solid rocket motor.
Let’s look at the point of ignition.
On both the motor and ELRC, the point of ignition is opposite the nozzle end.
Rocket motor: The reason for ignition at the top of the motor is due to the considerably faster rate at which the propellant grain is fully ignited. This is because the high pressure/high temperature gases are only able to escape through the nozzle of the motor, therefore, the flame channel burns downwards, not upwards.
ELRC: The point of ignition located in the rearward most end is due to simplicity of adaptation. However, later I will explain why this characteristic is so important to future ELRC development.
Let’s look at the propellant charge.
Solid rocket propellants burn at similar rates as compared to slow burning rifle powder.
(This characteristic only applies to cartridges filled to 90% or more.)
Rocket Motor: The propellant grain is the fuel that is consumed in the combustion process to produce the high-pressure gases that propel the rocket upward. The fuel burns slowly and typical KNO3 motors maintain a pressure of around 3000 PSI in the motor. To successfully make a rocket fuel burn and hold a set pressure, you have to regulate the surface area of the burning grain. As you can imagine, there is no way to “throttle” a burning hunk of propellant because it is made with both the fuel and oxidizer in it. They will burn underwater, or in space. Therefore, since there is no effective way of controlling how much of the grain is burning, we have to get a little more creative. As a rocket fuel grain burns, it is also eroding and flowing out into the atmosphere. Most high power rocket motors use a Bates style fuel grain. This is a tube made of fuel with very thick walls. It will burn on the top face, bottom face, and on the inner diameter of the grain. As the grain burns, the inner diameter grows. This increases the surface area. However, while the inner diameter is eroding and gaining surface area, the top and bottom are also eroding. This shortens the overall length of the grain; reducing the length of the inner diameter. This makes the grain burn a constant surface area, thereby keeping the internal motor pressure stable, and the thrust curve is therefore more linear. ELRC: The powder is burnt in an elliptical wave front that moves down the length of the cartridge. Not all of the powder is burnt in the cartridge however. Because the wave is creating pressure at the rear of the cartridge, this pushes the remaining powder against the projectile and pushes it out of the cartridge. As the wave front pushes the powder and projectile down the barrel, the powder is consumed. Because the powder is burning in a single wave plane, the surface area remains constant with the exception of the change of the diameter from body to bore.
Let’s look at the nozzle/neck:
Rocket motors and ELRC’s have a divergent cone shape that plays a significant role in performance.
Rocket Motors: The high-pressure gases produced by the consumption of the propellant create a subsonic flow toward the exit/nozzle. When the gases reach the nozzle, they are accelerated by the convergence of the nozzle. The gas velocity reaches several Mach numbers in the smallest area of the convergent section. As the gases exit the convergent section, they expand to many times their original volume in the divergent section of the nozzle as they are released to atmospheric pressures. It is this expansion in the divergent section of the nozzle that produces the vast majority of the thrust on the rocket.
ELRC: The cartridge has a cylindrical area known as the body, followed by a convergent section known as the neck. The neck angle plays a large role in the efficient burning of the powder. I will explain this more later. Design characteristic similarities
When firing your gun, the velocity of your projectile is directly related to the pressure and velocity of the propellant gases. If you could imagine your gun as being a rocket motor with a cylindrical section between the convergent and divergent section, you can see how rocket motor design theories can be applied to optimizing ELRC. The one limitation to this is that the rifle powder is not burned while only in the containment of the cartridge. This can create issues with optimizing neck angles due to an inconsistent burning surface area during the cartridge to bore diameter transition. The inherit similarity in ignition position affords us the luxury of easy development of solid single grain rifle propellants. The physical restriction of rifle powder to the area of the cartridge allows us to take advantage of controllable burning surface area (constant or adaptive pressure transient) and convergent nozzle gas acceleration. In general, rockets reach flight speed and hold somewhat steady at a velocity until the grain becomes structurally unstable and begins to burn out. This requires a constant pressure to avoid detonation during flight. Both rifle powder and rocket fuel burn at a rate that is proportional to the ambient pressure. This means that if a rocket nozzle is too small or a rifle bore is too small, it will build pressure exponentially until it exceeds that of the containing vessel (rocket motor case/rifle chamber). I have witnessed this first hand from 3 feet away when a kno3 rocket motor detonated at upwards of 150000 psi. Lots of blood and a few stitches inevitably followed.
In a rifle however, as the bullet is accelerated down the barrel, the volume for the expanding gases increases proportionally with the projectile velocity. This means that a constant propellant burn rate creates a downward sloping pressure transient. This, in effect, means the projectile acceleration slows down proportionally to the distance from the throat.
With this in mind, it would be advantageous for the design of an ELRC to incorporate an accelerating rate of propellant consumption to make projectile acceleration constant. I have tried several different experiments with this, but thus far, none have been acceptably safe or effective. In doing research on military experiments and development of current munitions, I have come up with a reasonable solution that is tried and currently in use across the world. I will discuss this in summary at the end.
The next linear characteristic design element is the optimization limits of ELRC’s
All ELR rounds have an optimum design that is fundamentally defined by the volume of propellant in the case. This means that no matter what cartridge you are firing, there is a set of design characteristics that is proportionally dependent on powder volume. Let me explain this. If you look at the 300 rum in performance, you will find max velocities around 3400 fps for light bullets and 2800 for the heavy bullets. If you were to balance out velocity with mass energy storage in the projectile, you would find an optimum weight bullet that defined the range usage of the cartridge. As a quick note, heavier Is not always better, as some would believe, however, mass does maintain velocity down range. This cartridge has now met its optimum design and cannot perform any better. Now we will look at a round that out performs the 300 rum; 338CT. This case has additional capacity and therefore more energy available for acceleration. If you were to optimize this cartridge with the perfect bullet, you would find a relationship between powder volume and bullet mass with respect to the 300 rum. This proportional relationship between powder volume and projectile mass from one cartridge to another, allows the design of ground breaking cartridges that are based on currently optimized designs. In effect, one could use these relationships to “scale” current rounds to any range capability they desired. Optimization of current cartridges with current technology
Take a quick look at a tank cannon. The M1 Abrams is armed with a Rheinmetall 120mm smoothbore cannon. This cannon is capable of 5200fps and an effective range of 4400y-8700y (depending on the load). If you scale this cartridge down using the previously discussed relationships, you would find a massive discrepancy in useable range. This is where my discussion of the similarities of rockets and firearms comes into play. Tank rounds have a flash tube that the ignition flame propagates thru. This creates a cylindrically expanding surface of burning propellant. Because it burns in an expanding cylinder, the volume of expanding gases grows exponentially. This exponentially increasing volume of gas creates a constant acceleration throughout the length of the barrel. Unlike conventional ELRC’s the tank projectiles accelerate to a higher final velocity with respect to propellant volume. Optimization of ELRC’s with a flash tube could theoretically increase the useable range of the cartridge. The other aspect that effects the efficiency difference in tank rounds is that the propellant is for the most part (from what little I know) contained and burned in the cartridge. This allows the subsonic propellant gases to be accelerated in the convergent bottleneck section to bore velocities high enough to achieve 5200fps+. Incorporating fixed propellant in ELR rounds will not only effect a higher muzzle velocity, but will also reduce fouling. When the powder in conventional ELRC’s is burned down the bore, it deposits carbon and binding compounds in the rifling. This fouling can be minimized by the extreme temperatures exhibited at the convergent bottleneck of the cartridge. Because of the flame pressure front burning in a radial direction, the binding compounds would be more prone to affixing themselves to the cartridge wall. This will increase barrel life, aswell as increasing the intervals between cleaning.
In summary
I am theorizing that once a round is optimized with current tank round technology, it can be effectively “scaled” to any desired size needed to reach a specific target range. Ok, so I’ve been writing this for the last 5 hours… so I’m getting tired and lazy. Hence the 1 sentence summary.
Please correct me on any facts I may have wrong. I’m no expert on this, so there are bound to be flaws in my logic. If you have any insight into my theory, please speak up. I want to begin development of an extremely efficient scalable round for elr. Thanks for sticking with me and reading this…. If you made it to the end, you have a longer attention span than me…..