Years ago, before 6 CM brass could be bought and the 22 CM was a true wildcat I had to neck down 6.5 Creedmoor brass, and with no dies available I had to stuff new internals into parent case dies to load my 22 Creedmoor.
The Hornady micrometer top seater would not allow me to get cam over at the die base like my Redding or Forster dies will. There was no 'positive stop' to seat bullets to. I could only rely on the feel when the die bottomed out on the neck of the brass. I wanted to get all the length growth the I could with firing to close up the gap the the chamber transition after I measured the overall chamber length. I ended up with a few thou of variance in case length which then affected my seating depth accordingly. And then there were a few crushed shoulders.
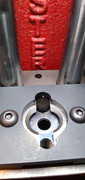
Unhappy with inconsistent seating depths and a bit of time pondering a fix, I looked twice one day at the hole behind the guide rods on the press table. I found a 3/16" (.1875") drill bit would go into it like a glove. After a bit of measuring, armed with calipers I set off the the hardware in search of the 'fix' for the positive stop probem. With the shank on a 10x32 cap head screw measuring .186 I felt I had a fix. I picked up a cap screw 1.5" long, 2 nuts and 2 flat washers. With the threads being a tickle over the .1875" I had to chuck the screw into my cordless drill and turn it in 200 grit emery cloth for a couple of seconds to make the fit work. I ran the first nut to the shoulder, then flat washer with another nut as a jamb nut. The 2nd flat washer lays on the press table to provide more surface area than the nut when the press 'bottoms out' against my new positive stop. This provides the stop before the die makes neck contact with the brass. At the time, I picked up and made a second one with a 2" cap screw for about an inch of total thread adjustment length depending on case length if I used this setup for longer cases in the future. I simply slip it out when not using this seating die.
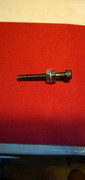
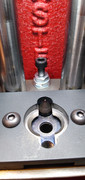
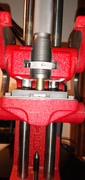
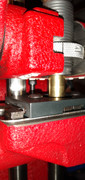
I now get consistent seating depths to within .0005 when measuring CBTO with my Mitutoyo calipers!
The Hornady micrometer top seater would not allow me to get cam over at the die base like my Redding or Forster dies will. There was no 'positive stop' to seat bullets to. I could only rely on the feel when the die bottomed out on the neck of the brass. I wanted to get all the length growth the I could with firing to close up the gap the the chamber transition after I measured the overall chamber length. I ended up with a few thou of variance in case length which then affected my seating depth accordingly. And then there were a few crushed shoulders.
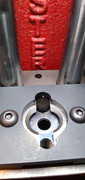
Unhappy with inconsistent seating depths and a bit of time pondering a fix, I looked twice one day at the hole behind the guide rods on the press table. I found a 3/16" (.1875") drill bit would go into it like a glove. After a bit of measuring, armed with calipers I set off the the hardware in search of the 'fix' for the positive stop probem. With the shank on a 10x32 cap head screw measuring .186 I felt I had a fix. I picked up a cap screw 1.5" long, 2 nuts and 2 flat washers. With the threads being a tickle over the .1875" I had to chuck the screw into my cordless drill and turn it in 200 grit emery cloth for a couple of seconds to make the fit work. I ran the first nut to the shoulder, then flat washer with another nut as a jamb nut. The 2nd flat washer lays on the press table to provide more surface area than the nut when the press 'bottoms out' against my new positive stop. This provides the stop before the die makes neck contact with the brass. At the time, I picked up and made a second one with a 2" cap screw for about an inch of total thread adjustment length depending on case length if I used this setup for longer cases in the future. I simply slip it out when not using this seating die.
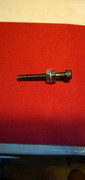
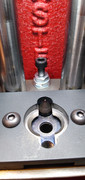
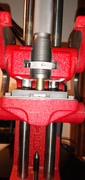
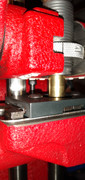
I now get consistent seating depths to within .0005 when measuring CBTO with my Mitutoyo calipers!
Last edited: