I'm a home shop gunsmith, I have had some professional machining education, but don't be fooled this is a hobby for me. I have chambered a total of about 6 guns up until this one all short action chambers. I have had good results. All of my rigs out shoot me by a long stretch, most when I do my part are better than 1/2 moa guns.
Two years ago I started a .300 Win Mag project based on a Stainless Factory 700. I trued the action, and went with a 1 piece PTG bolt that got NP3 treated.
When I chambered the magnum I ended up with some run out in the chamber. Best I could tell it was around .005-007" ish. I was disappointed in how the project turned out, that combined with the lack of components (Still!) put the project in mothball mode. Initial testing was inconclusive as I shot approximately 30 rounds which all printed 1 moa ish. Well now I want to get it back up and running.
If I were to rebarrel the gun, I need to learn what I did wrong the first go around. Let me describe my process. I want to improve my process as much as I can.
1. Warm up lathe for approx 20 minutes
2. Align barrel in lathe with PTG Range Rods zeroing both ends to within .0005" I chamber through the headstock. I use copper penny's between the jaws and barrel and spider.
3. Machine shoulder, threads, counter bore.
4. Cut chamber with PTG Tac Match .300 Finish Reamer. I use the bushing model which I select a bushing to be within .0002" or so.
5. I push the reamer with a floating holder which allows for up to .025" of misalignment.
6. The reamer is held by a modified tap wrench which is square to the above floating holder.
7. I cut the Chamber .025-.050" at a time withdraw the reamer and clean everything. Re-oil and repeat.
8. I cut at around 45-60 rpm
9. I cut this until I get within .025 of finish depth. I will then cut .010 and the final few thousands, making sure to clean really good between the last cuts.
10. Double check headspace
11. Flip it around, crown, thread, Etc
Here's a few shots
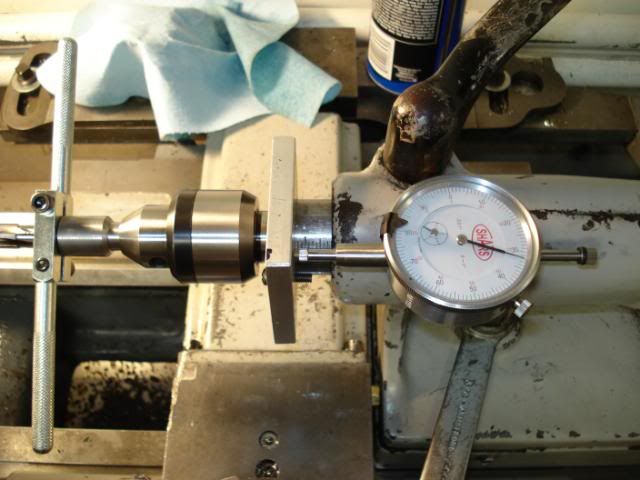

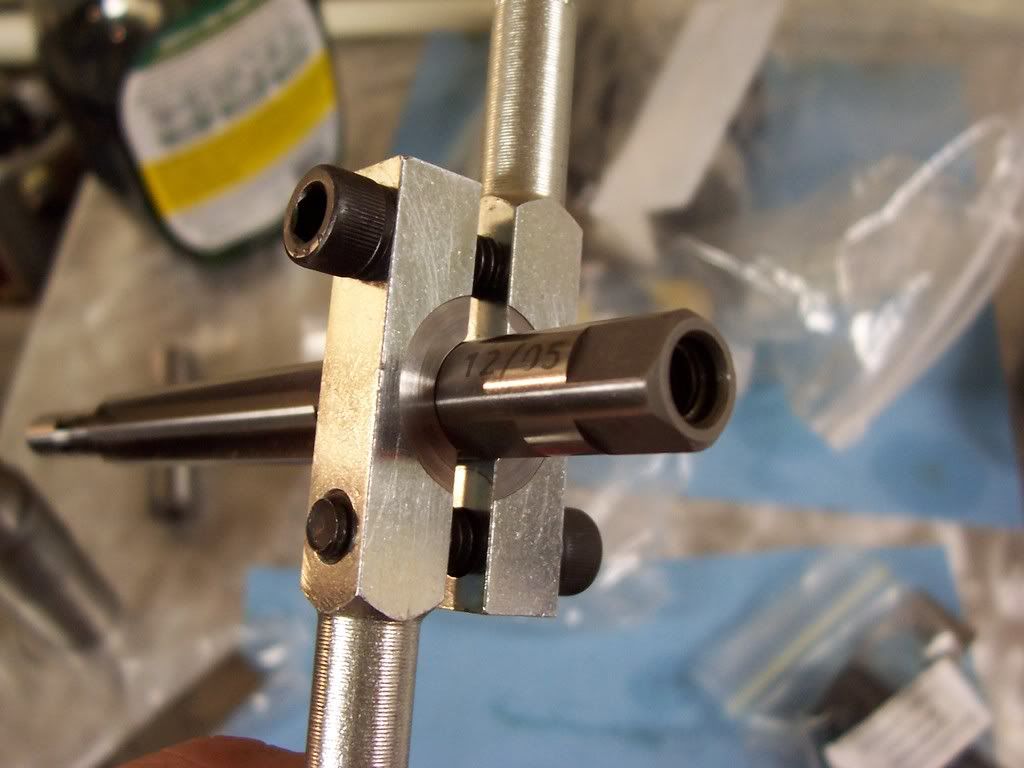

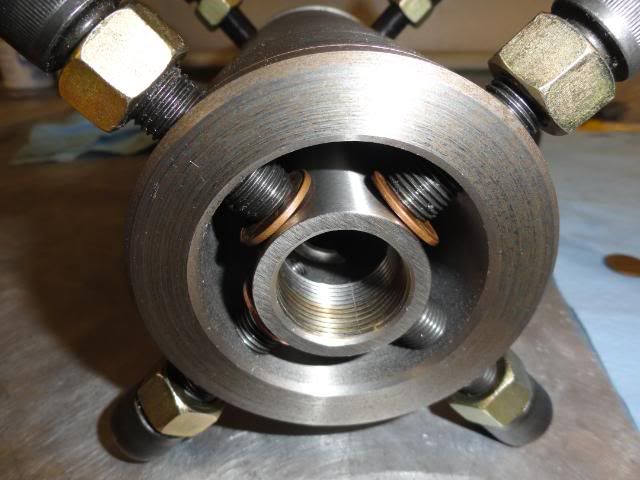
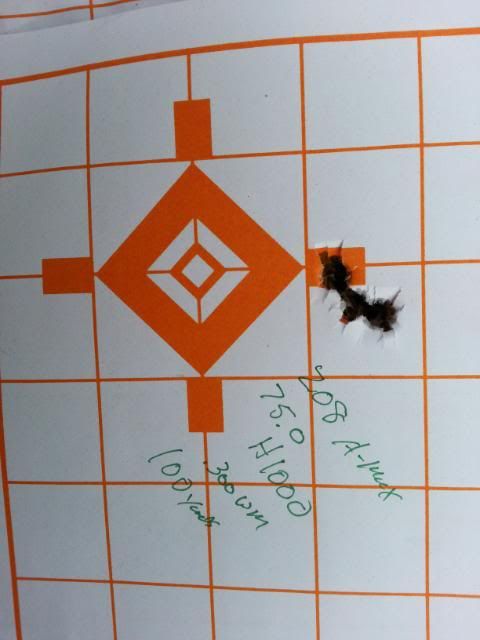
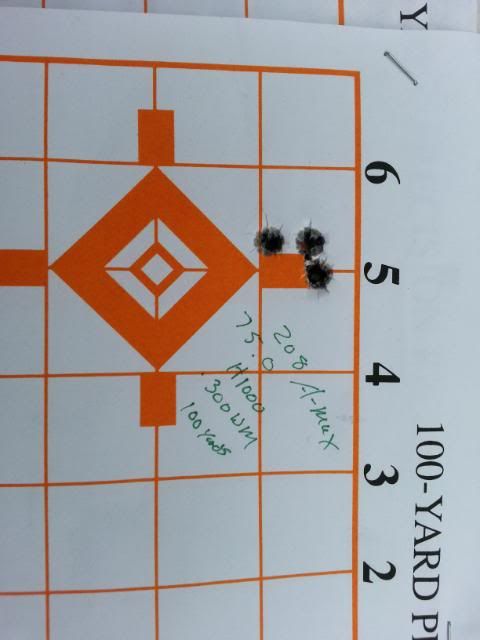
Please help trouble shoot my process, methods, etc
I have been thinking it's one thing to do this with a short .308 style cartridge. But for this big of a chamber I could probably drill, true that with a boring bar and then use the finish reamer. Thing is I would have to cut that on a taper to align the reamer and how does the bushing work if it's not in contact until after its cutting the body.
Please be brutally honest, if I'm being a tool here, throw me a bone and school me!
Thanks
Two years ago I started a .300 Win Mag project based on a Stainless Factory 700. I trued the action, and went with a 1 piece PTG bolt that got NP3 treated.
When I chambered the magnum I ended up with some run out in the chamber. Best I could tell it was around .005-007" ish. I was disappointed in how the project turned out, that combined with the lack of components (Still!) put the project in mothball mode. Initial testing was inconclusive as I shot approximately 30 rounds which all printed 1 moa ish. Well now I want to get it back up and running.
If I were to rebarrel the gun, I need to learn what I did wrong the first go around. Let me describe my process. I want to improve my process as much as I can.
1. Warm up lathe for approx 20 minutes
2. Align barrel in lathe with PTG Range Rods zeroing both ends to within .0005" I chamber through the headstock. I use copper penny's between the jaws and barrel and spider.
3. Machine shoulder, threads, counter bore.
4. Cut chamber with PTG Tac Match .300 Finish Reamer. I use the bushing model which I select a bushing to be within .0002" or so.
5. I push the reamer with a floating holder which allows for up to .025" of misalignment.
6. The reamer is held by a modified tap wrench which is square to the above floating holder.
7. I cut the Chamber .025-.050" at a time withdraw the reamer and clean everything. Re-oil and repeat.
8. I cut at around 45-60 rpm
9. I cut this until I get within .025 of finish depth. I will then cut .010 and the final few thousands, making sure to clean really good between the last cuts.
10. Double check headspace
11. Flip it around, crown, thread, Etc
Here's a few shots
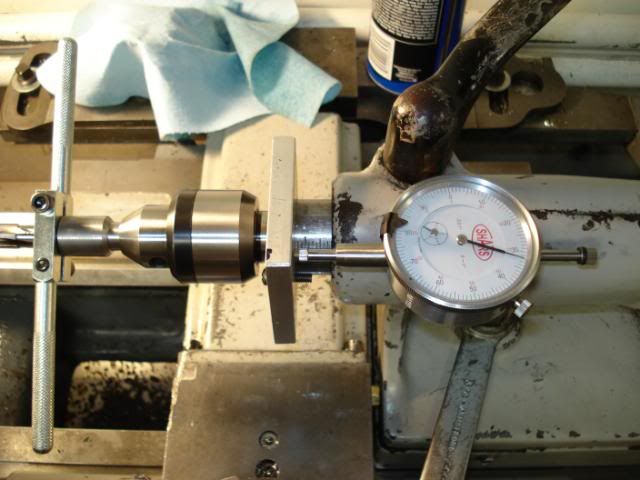

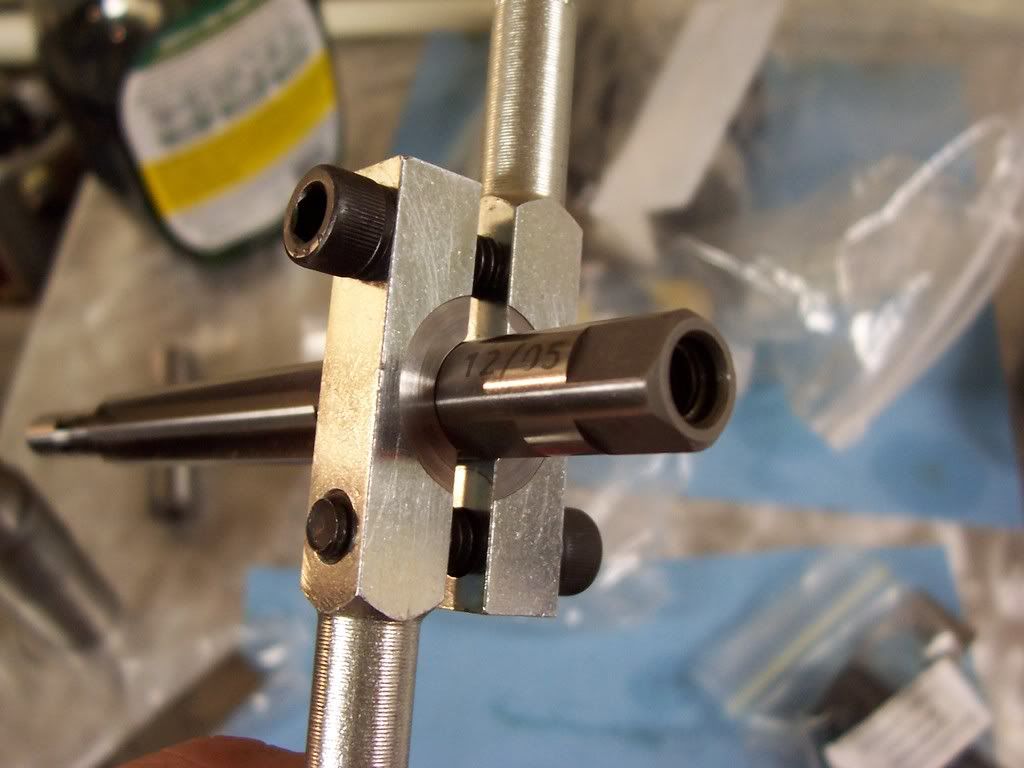

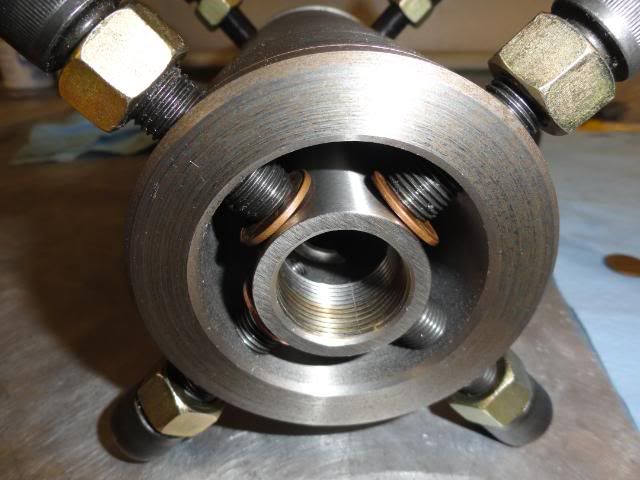
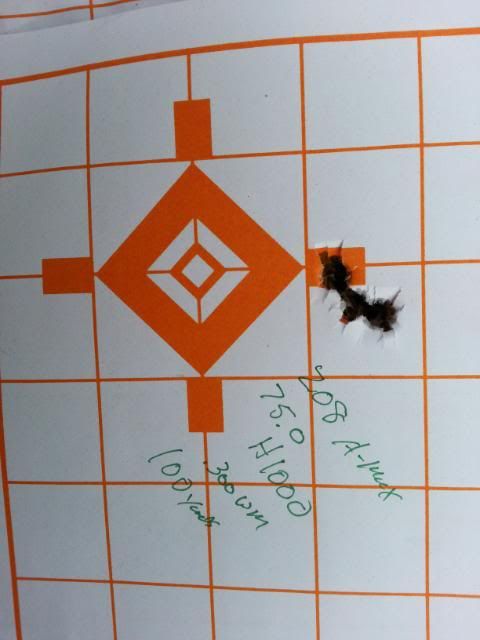
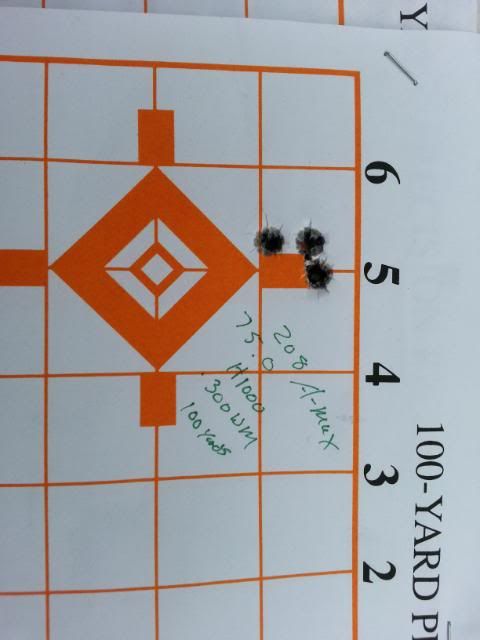
Please help trouble shoot my process, methods, etc
I have been thinking it's one thing to do this with a short .308 style cartridge. But for this big of a chamber I could probably drill, true that with a boring bar and then use the finish reamer. Thing is I would have to cut that on a taper to align the reamer and how does the bushing work if it's not in contact until after its cutting the body.
Please be brutally honest, if I'm being a tool here, throw me a bone and school me!
Thanks