i have spent some time looking into this topic and have stumbled upon thickness's i should use to handle the muzzle gas pressure of a sub sonic 300 blackout. i have seen some numbers posted and will add a safety factor to it also. i will ask for additional feedback when time draws closer.
as of now i think having the main tube threaded on the exterior with the end caps having internal threads will be stronger. i would prefer to have a internal threads on the main tube so that the exterior profile is flat but i need to be sure the design would be strong enough. this will depend upon how much material is left after thread are cut and also how many thread will be responsible to hold the pressure spike. i found literature that mentions how thick to cut thread without compromised material to much.
the baffles are already figured out with the exception of whether i would like to have the k baffles stepped or not. part of me says to make them stepped even though i have not seen any(?) k baffles with stepped 60 degree cone. the stepped should encourage more turbulence and slow down the expanding gases more -> reducing decibels.
i will probably keep only leading k baffle stainless and the remaining some form of aluminum; 6061 t6 or maybe 7075.
although all advice is welcome here is the more specific questions i have concern the end cap that attaches to threaded barrel:
here is an crude image to illustrate what i am thinking.
the grey annotation would be a stainless steel tube that will have many smaller ports in it to reduce the change of pieces of ss wool from falling into blast camber(?). the yellow annotations are stainless steel scrubbing pads i was thinking about using.
the end cap it self i would like to have some symmetrical large ports to promote gasses from exiting prior to the muzzle opening. i might build a small bell into the crown of the end cap to encourage some of gases to follow the walls to reduce it from then entering the center bore hole. i may even do something else different here to cause turbulence; i will think much more on these contradicting theories.
how common is it to have the gas exit out several holes in the other end cap? or do most prefer to just have center bore to exit gasses? ill post an image of what the other end cap will look like later.
i think there is enough here for critique and thanks for your time. i will update this as i continue to evolve this idea in my mind and on paper before i put into solidworks.
as of now i think having the main tube threaded on the exterior with the end caps having internal threads will be stronger. i would prefer to have a internal threads on the main tube so that the exterior profile is flat but i need to be sure the design would be strong enough. this will depend upon how much material is left after thread are cut and also how many thread will be responsible to hold the pressure spike. i found literature that mentions how thick to cut thread without compromised material to much.
the baffles are already figured out with the exception of whether i would like to have the k baffles stepped or not. part of me says to make them stepped even though i have not seen any(?) k baffles with stepped 60 degree cone. the stepped should encourage more turbulence and slow down the expanding gases more -> reducing decibels.
i will probably keep only leading k baffle stainless and the remaining some form of aluminum; 6061 t6 or maybe 7075.
although all advice is welcome here is the more specific questions i have concern the end cap that attaches to threaded barrel:
here is an crude image to illustrate what i am thinking.
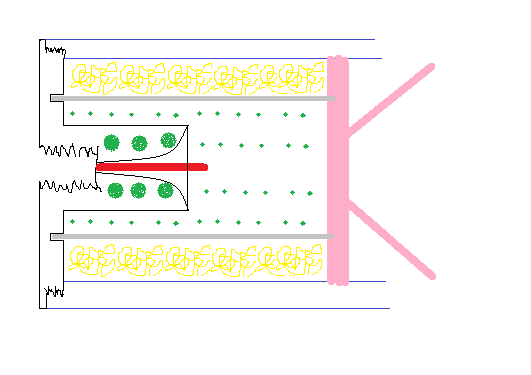
the grey annotation would be a stainless steel tube that will have many smaller ports in it to reduce the change of pieces of ss wool from falling into blast camber(?). the yellow annotations are stainless steel scrubbing pads i was thinking about using.
the end cap it self i would like to have some symmetrical large ports to promote gasses from exiting prior to the muzzle opening. i might build a small bell into the crown of the end cap to encourage some of gases to follow the walls to reduce it from then entering the center bore hole. i may even do something else different here to cause turbulence; i will think much more on these contradicting theories.
how common is it to have the gas exit out several holes in the other end cap? or do most prefer to just have center bore to exit gasses? ill post an image of what the other end cap will look like later.
i think there is enough here for critique and thanks for your time. i will update this as i continue to evolve this idea in my mind and on paper before i put into solidworks.