I just started using a benchsource annealer and I'm not sure if I set everything up right.
I put the flames so they are aimed towards right above the neck/shoulder junction. The inside blue blame is around 5/8" away from the center of the spinning piece (so a little less far from the brass itself)
It looks like with this configuration, I need about 2.8 seconds. Is that right?
I put 750 tempilaq on the inside and outside of the neck and 450 on the body. Here is a video of it:
If you can't see much on the youtube video, go here to see a slightly better one:
[video]http://s1133.photobucket.com/user/timelinex/media/20140530_164547_zpsa6e3e342.mp4.html[/video]
It looks like it goes clear, right before the machine takes it out of the flame. Here is apicture of it afterward, as you can see the 450 turns clear above halfway down the body, so thats good.
Here is a picture of a case annealed, without the tempilaq to discolor it:
How does that look? Is that right? I thought there would be a bluer hue to the annealed cases. Am I holding it in the flame too little or too much?
Thanks!
I put the flames so they are aimed towards right above the neck/shoulder junction. The inside blue blame is around 5/8" away from the center of the spinning piece (so a little less far from the brass itself)
It looks like with this configuration, I need about 2.8 seconds. Is that right?
I put 750 tempilaq on the inside and outside of the neck and 450 on the body. Here is a video of it:
If you can't see much on the youtube video, go here to see a slightly better one:
[video]http://s1133.photobucket.com/user/timelinex/media/20140530_164547_zpsa6e3e342.mp4.html[/video]
It looks like it goes clear, right before the machine takes it out of the flame. Here is apicture of it afterward, as you can see the 450 turns clear above halfway down the body, so thats good.
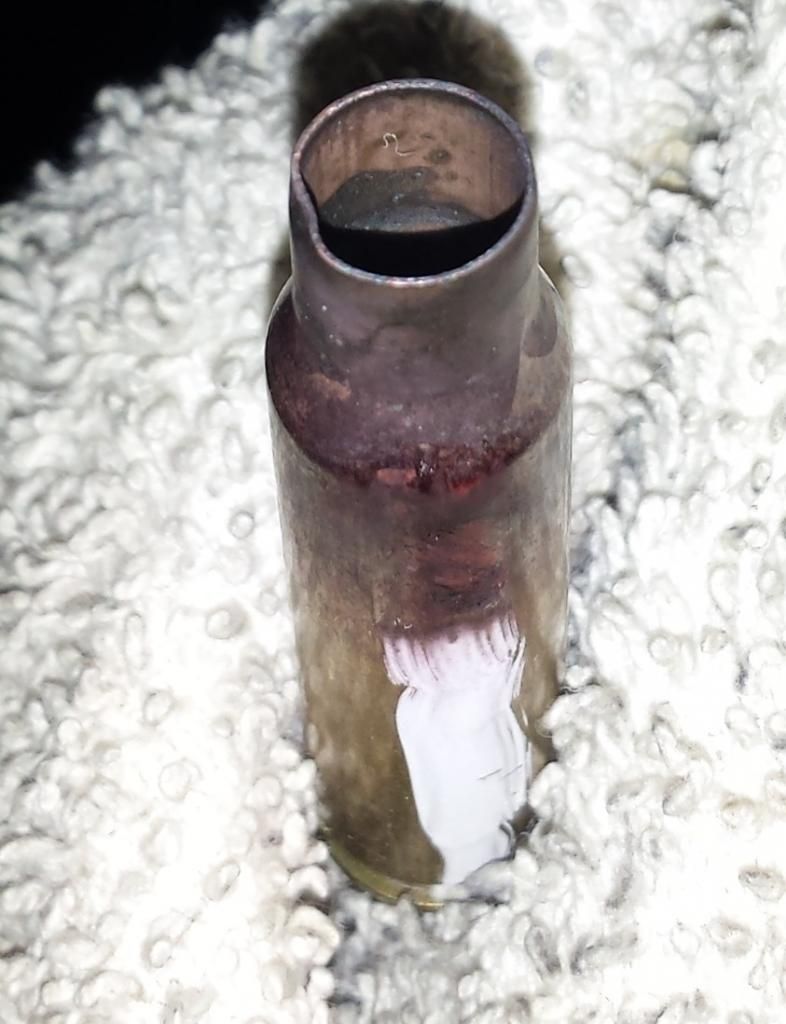
Here is a picture of a case annealed, without the tempilaq to discolor it:
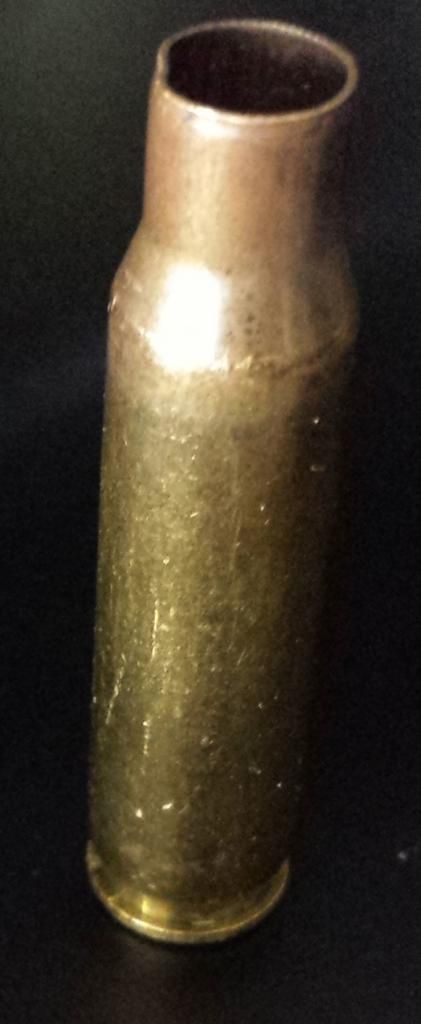
How does that look? Is that right? I thought there would be a bluer hue to the annealed cases. Am I holding it in the flame too little or too much?
Thanks!
Last edited: