Ok guys I need some advice to see if I am doing anything wrong. I bought a rougher and finisher reamer from PTG and they are made of HSS. I made a forming die first and I pre drilled the chamber and then proceeded to single point the 1 degree taper until I only had a few thousandths left. I then started to use my chamber reamer. I used Hangstifers oil (very thick stuff used for reaming and tapping) and had the piloted reamer in the piece of 4140 at RC 32 material with a live center on the back of the reamer with a large tap handle on the reamer that I would hold.
Now this reamer has a large diameter of 1.16" at the base (This is chambering a 20mm case necked down to a 50 cal). I wanted to keep the surface feet low so I started at 50 rpm. I would take .020 deep cuts between removing the reamer and clearing the chips. The first part of the reaming was just removing material at the neck and starting at the shoulder and it was working fine. But when the flutes started cutting at the 1 degree main angle of the chamber it really was grabbing (it makes sense just because there is approx 2.7" of flute length between the base and the shoulder). I ended up slowing down the lathe to 35rpm and fed it really slow (approx .010" per minute) and it would bite so hard sometimes that the tap handle would rip out of my hands.
Ok here is the main point I am trying to convey. One of the times when it ripped out of my hands I stopped the lathe and just torqued on the handle (not actually turning the reamer to cut, but to load it up) and while I was torquing on the handle I noticed that the reamer was really flexing (approx 8 degrees). I pulled the reamer out and cleaned everything up and felt the chamber and it had no galls in it and the flutes were still sharp (This is a brand new reamer). I lubed everything up again and put the tap handle on the compound so I don't have to hold it anymore. Well, when feeding it in the reamer broke.
It was a pain in the ass getting it out but when I looked at the end of the reamer it looks to me most of the material was taken away for the flutes making the strength of the reamer itself weak. The core diameter is approx .4". I would think trying to turn a 1.1" diameter with only a .4" core is too much stress. Do you guys think that could be the case or am I just doing something wrong?
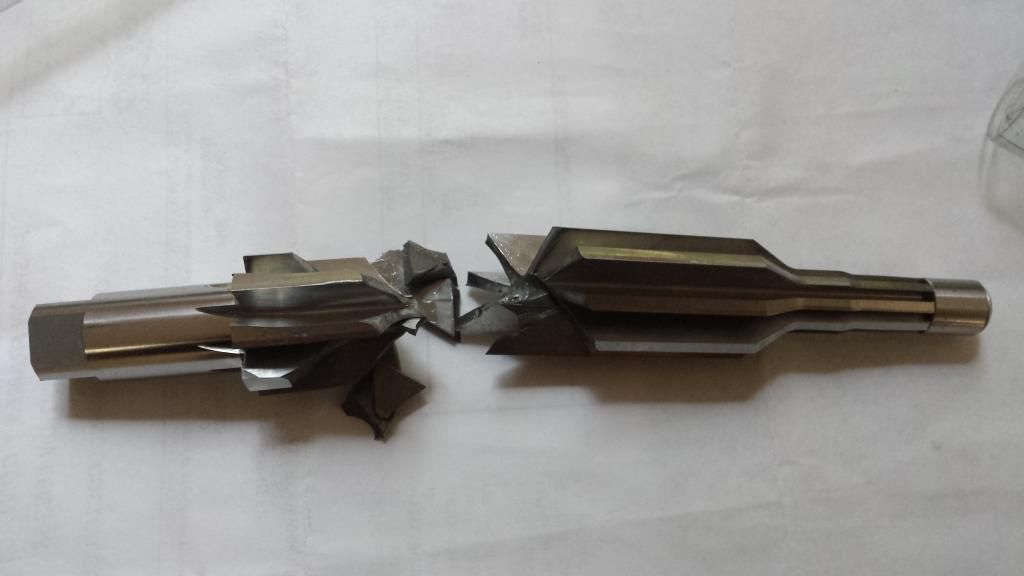
You can see that there really isn't mutch material there for the reamer to have any strength. It looks to me that it was all removed for the flutes.

Now this reamer has a large diameter of 1.16" at the base (This is chambering a 20mm case necked down to a 50 cal). I wanted to keep the surface feet low so I started at 50 rpm. I would take .020 deep cuts between removing the reamer and clearing the chips. The first part of the reaming was just removing material at the neck and starting at the shoulder and it was working fine. But when the flutes started cutting at the 1 degree main angle of the chamber it really was grabbing (it makes sense just because there is approx 2.7" of flute length between the base and the shoulder). I ended up slowing down the lathe to 35rpm and fed it really slow (approx .010" per minute) and it would bite so hard sometimes that the tap handle would rip out of my hands.
Ok here is the main point I am trying to convey. One of the times when it ripped out of my hands I stopped the lathe and just torqued on the handle (not actually turning the reamer to cut, but to load it up) and while I was torquing on the handle I noticed that the reamer was really flexing (approx 8 degrees). I pulled the reamer out and cleaned everything up and felt the chamber and it had no galls in it and the flutes were still sharp (This is a brand new reamer). I lubed everything up again and put the tap handle on the compound so I don't have to hold it anymore. Well, when feeding it in the reamer broke.
It was a pain in the ass getting it out but when I looked at the end of the reamer it looks to me most of the material was taken away for the flutes making the strength of the reamer itself weak. The core diameter is approx .4". I would think trying to turn a 1.1" diameter with only a .4" core is too much stress. Do you guys think that could be the case or am I just doing something wrong?
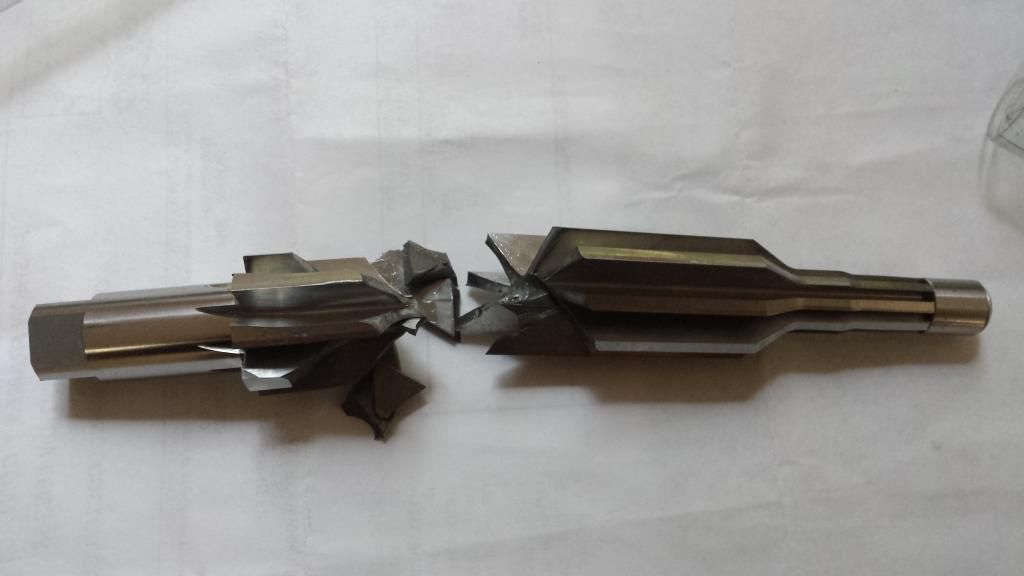
You can see that there really isn't mutch material there for the reamer to have any strength. It looks to me that it was all removed for the flutes.

Last edited: