The first run of the PLC controlled 1050 was a success. Along with the auto drive I added a PLC that controls the motor. There is an up and down limit switches that are on a clock so if the tool head doesn’t reach either in the allotted time the timer times out and stops the motor, this keeps the clutch from continually slipping if a jam occurs. I went ahead and made the upper limit switch a round counter to count the number of completed rounds.
I then tied into the powder check die and low primer systems so the machine would halt operation if there were a high/low charge or no primers in the tube. I programmed a routine into the PLC that would count down from 100 to start with and reset every time the low primer alarm was triggered. This way all the operator has to do is fill the tube and press the run button and the screen is automatically reset..
To finish up there will be proximity switches on the bullet/case tubes and powder measure to stop operation if any of them run low. Then build an enclosure for the PLC and display and find something else to tinker with.
I then tied into the powder check die and low primer systems so the machine would halt operation if there were a high/low charge or no primers in the tube. I programmed a routine into the PLC that would count down from 100 to start with and reset every time the low primer alarm was triggered. This way all the operator has to do is fill the tube and press the run button and the screen is automatically reset..
To finish up there will be proximity switches on the bullet/case tubes and powder measure to stop operation if any of them run low. Then build an enclosure for the PLC and display and find something else to tinker with.
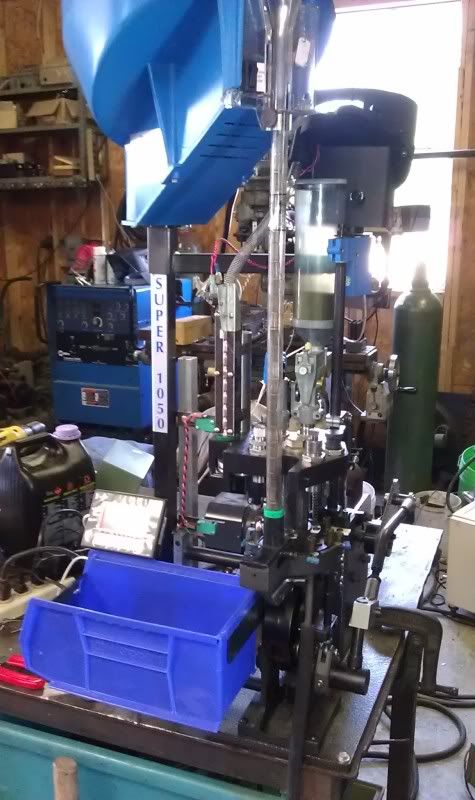
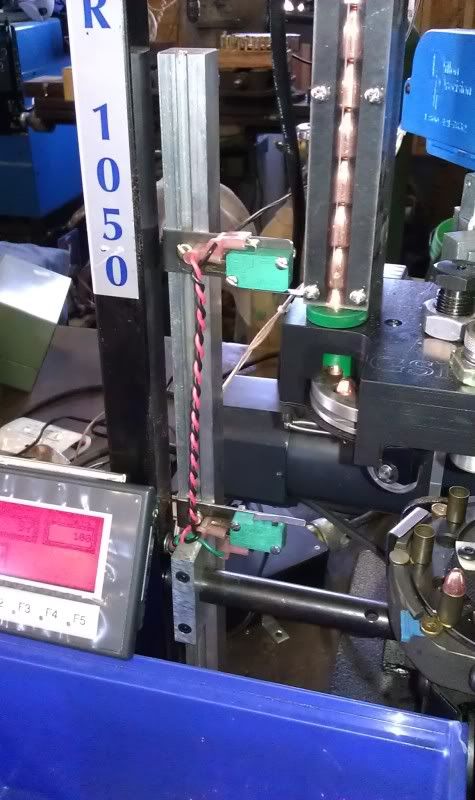
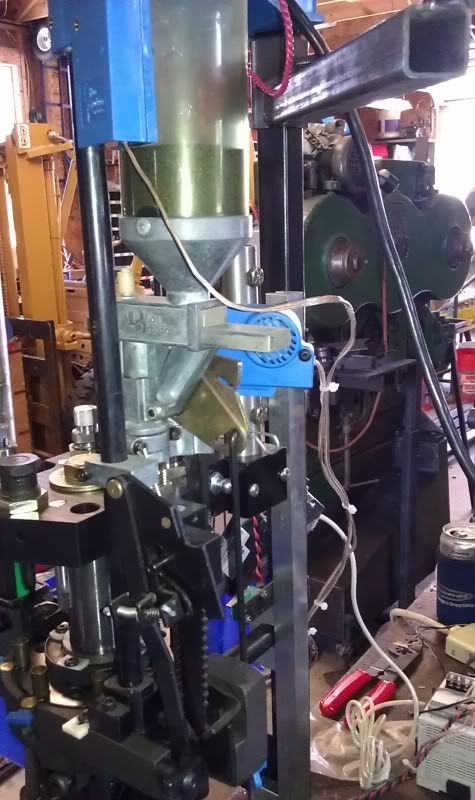
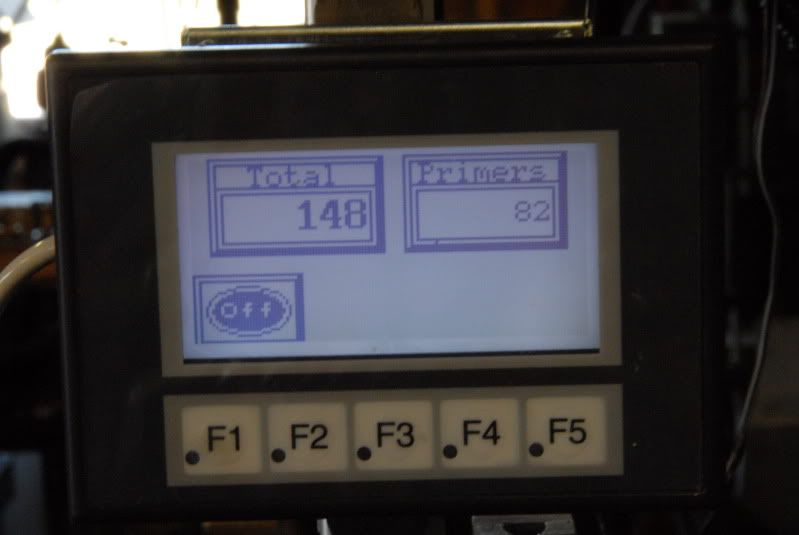