I've done 30 or so CZ452 handles here in Australia, and they're hard bastards.
I linish/grind the ball into a shaft around 8mm dia, then carefully grab it in the lathe on that 8mm dia shaft, turn it carefully and 'true' the diameter to 6mm (put a little shoulder on it where the thread should finish), then linish the end that was in the lathe to match the perfectly machined diameter, put a slight taper on it, then run an M6 die over it to put a thread on it. I'll try supply some pics to make it clearer.
I tried making a jig to make it quicker, as the grinding/linishing is the real crap part of the job, It takes about 15-20mins with a 40grit belt to make a rough shaft to work with, making sure I dunk it in water to cool it off. Problem with the jig was that STILL each bolt handle is different and I have to end up ditching the jig because it won't make the thread centre on EVERY handle.
I can't produce them fast enough to keep up with demand, which sucks because there are heaps of people after them.
The knob I screw onto the handle is a CNC machined Aluminium knob, slightly smaller than your standard badger style knob (scaled down basically).
I should mention that because they're a cast handle, there are holes/pores/air pockets in the casting 99% of the time... You might see it in the first pic, I have to fill these holes with Silver Solder, re-linish/machine, then they're threaded.
The whole thing is blasted and Cerakoted/baked because the blueing is long gone by the end.
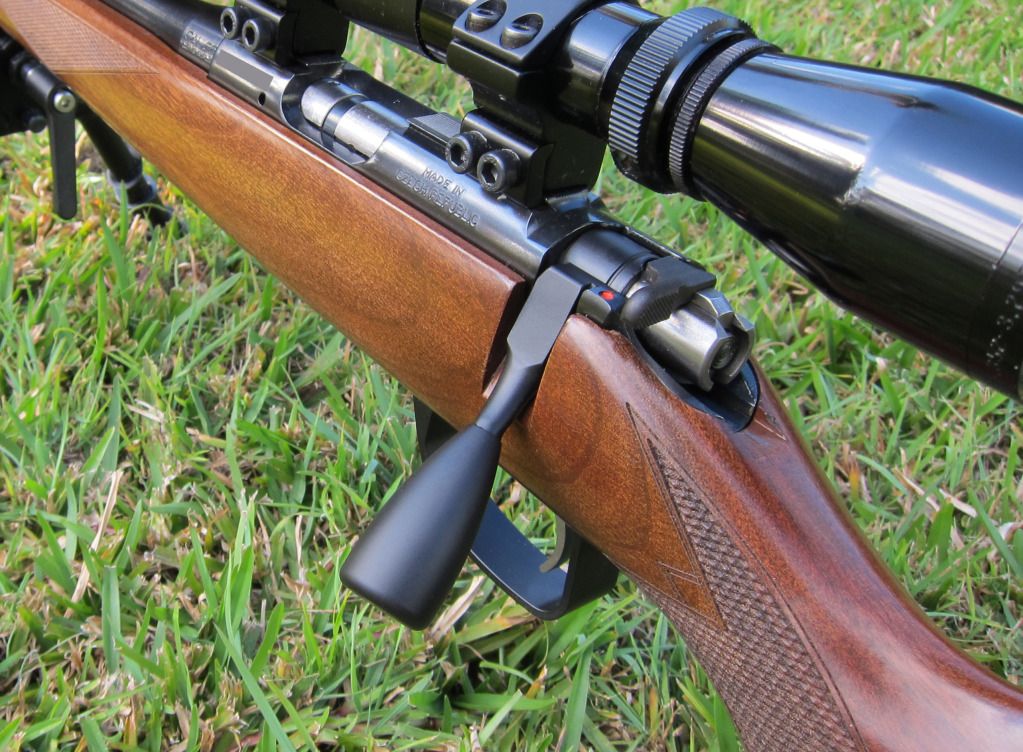