I try to avoid bringing a trinket to market solely for the purpose of complicating someones purchasing decision. Rarely am I guilty of an original thought, so often the stuff I do is an attempt to improve upon an existing design.
The Badger EFR mount does a number of things very well. The limitation of the part is that outside the intended application, it's basically unusable. Tactical rifles are great and a lot of fun. So is killing critters that need killing. Feral piggys and mangey coyotes likely occupy the top of that list.
So with that comes the target audience for what our EFR mount is for. Folks desiring a lighter weight gun in a slimmer package, yet still fitted with the option of being able to run at night with peripheral optics. That problem statement opened Pandora's box as it brought a number of other things to the table that I've wanted to change.
Before going into this, one has to understand the original intent of the Badger EFR mount. My recollection is that the piece came about for military applications. The military is a shining example of simplification and delegation. In the Marine Corps one form of this is known as the "echelon levels of repair/maintenance."
Take a basic rifle for instance. 1st echelon repair/maintenance is at the operator level. Keep it clean, oiled, and free of corrosion. If something is lost or it breaks, report it. This tier level increases to where a guy is making components from raw materials. (there is a point to this, I promise)
In the case of an XM3 or M-whatever, the operator is unlikely to be peeling barreled actions from stocks as that would be a violation of the repair echelon. That chore is generally reserved for armorer's, 2112's etc. So, when you look at the original EFR mount, the 6 little screws holding it together were a non issue. Everything pretty much stayed together.
Now, fast forward to today. If your rifle has one of these, at some point someone (other than myself) has likely uttered a couple expletives when confronted with busting the top half off one these things. Do it for a living and it soon becomes a chore you'll associate as an itch on the top of your foot, while wearing tightly laced boots, and standing an inspection in the August sun somewhere humid.
-it just sucks...
So, that was the first problem I set out to solve.
Because I get to make stuff however I want, our new UL EFR for Varmint hunting is tailored for narrower gun stocks and features a hinge mechanism that retains the entire unit in the rifle stock. One removes two screws, tips the top half up/away, and the barreled action will peel right out.
Because I know someone will ask: What about the hinge and what about recoil?
I confronted this challenge two ways. I doubled up on the recoil lugs present in the base piece. Next, I machined the hinge assembly so that it pinches on itself as you button it down with the screws. The pin becomes "loaded" so that the joint is locked. -Last thing I wanna be on the hook for is someone "Peter Panning" their expensive optic out of a tree stand after a shot.
With a lighter platform being the objective, we kept the barrel contour provision constrained to a Remington Varmint profile. The ID of the bore is 1.050". Additionally, strategic use of an endmill was employed to remove weight wherever feasible.
Bedding the unit in the rifle stock is pretty easy and the lattice work on the bottom promotes good adhesion combined with mechanical bonds once the resin system cures. The pockets on the bottom are dovetailed to capture the epoxy. At only 1.375" wide, it's much easier to graft it into a narrower forend.
We make these on our new 5 axis machine. It's nice because it offers the powerful tool of work holding consolidation. We can present the part to the spindle a number of different ways in a single setup. Doing so mitigates the risk of errors from switching it from one vise to another.
The STENAG rail geometry is gauged and qualified. That tool is awesome, takes all the guess work out.
Weight 3.4oz minus the two screws. (those arrive tomorrow) Overall dimensions are 5" x 1.375" x 1.680".
Hope you like it.
C.
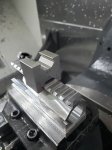
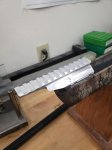
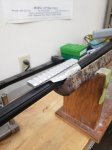
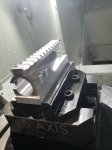
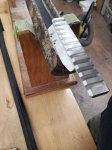
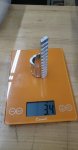
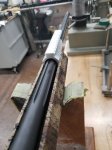
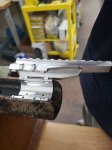
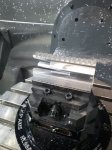
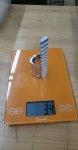
The Badger EFR mount does a number of things very well. The limitation of the part is that outside the intended application, it's basically unusable. Tactical rifles are great and a lot of fun. So is killing critters that need killing. Feral piggys and mangey coyotes likely occupy the top of that list.
So with that comes the target audience for what our EFR mount is for. Folks desiring a lighter weight gun in a slimmer package, yet still fitted with the option of being able to run at night with peripheral optics. That problem statement opened Pandora's box as it brought a number of other things to the table that I've wanted to change.
Before going into this, one has to understand the original intent of the Badger EFR mount. My recollection is that the piece came about for military applications. The military is a shining example of simplification and delegation. In the Marine Corps one form of this is known as the "echelon levels of repair/maintenance."
Take a basic rifle for instance. 1st echelon repair/maintenance is at the operator level. Keep it clean, oiled, and free of corrosion. If something is lost or it breaks, report it. This tier level increases to where a guy is making components from raw materials. (there is a point to this, I promise)
In the case of an XM3 or M-whatever, the operator is unlikely to be peeling barreled actions from stocks as that would be a violation of the repair echelon. That chore is generally reserved for armorer's, 2112's etc. So, when you look at the original EFR mount, the 6 little screws holding it together were a non issue. Everything pretty much stayed together.
Now, fast forward to today. If your rifle has one of these, at some point someone (other than myself) has likely uttered a couple expletives when confronted with busting the top half off one these things. Do it for a living and it soon becomes a chore you'll associate as an itch on the top of your foot, while wearing tightly laced boots, and standing an inspection in the August sun somewhere humid.
-it just sucks...
So, that was the first problem I set out to solve.
Because I get to make stuff however I want, our new UL EFR for Varmint hunting is tailored for narrower gun stocks and features a hinge mechanism that retains the entire unit in the rifle stock. One removes two screws, tips the top half up/away, and the barreled action will peel right out.
Because I know someone will ask: What about the hinge and what about recoil?
I confronted this challenge two ways. I doubled up on the recoil lugs present in the base piece. Next, I machined the hinge assembly so that it pinches on itself as you button it down with the screws. The pin becomes "loaded" so that the joint is locked. -Last thing I wanna be on the hook for is someone "Peter Panning" their expensive optic out of a tree stand after a shot.
With a lighter platform being the objective, we kept the barrel contour provision constrained to a Remington Varmint profile. The ID of the bore is 1.050". Additionally, strategic use of an endmill was employed to remove weight wherever feasible.
Bedding the unit in the rifle stock is pretty easy and the lattice work on the bottom promotes good adhesion combined with mechanical bonds once the resin system cures. The pockets on the bottom are dovetailed to capture the epoxy. At only 1.375" wide, it's much easier to graft it into a narrower forend.
We make these on our new 5 axis machine. It's nice because it offers the powerful tool of work holding consolidation. We can present the part to the spindle a number of different ways in a single setup. Doing so mitigates the risk of errors from switching it from one vise to another.
The STENAG rail geometry is gauged and qualified. That tool is awesome, takes all the guess work out.
Weight 3.4oz minus the two screws. (those arrive tomorrow) Overall dimensions are 5" x 1.375" x 1.680".
Hope you like it.
C.
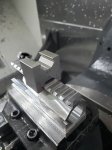
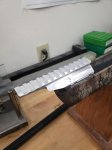
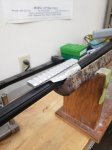
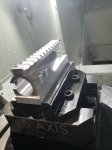
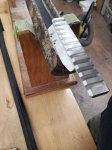
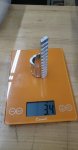
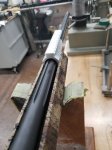
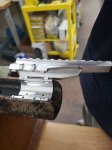
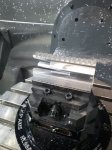
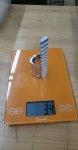
Last edited: